Mill for Seawolf project dismantled at Y-12
A poster produced in the 1990s paid tribute to the Seawolf submarine.
The removal of a big machine at Y-12’s Alpha-1 facility is a big deal.
A large mill used to produce the first propulsor for the legendary Seawolf submarine has been dismantled. It took three years for Y-12 to build the propulsor, but only a few months to take down the machine used for the project.
In 1989, the U.S. Navy launched a plan to build the propulsor for the then new Seawolf. The propulsor is the device used to propel a marine vessel, which includes the propellers, water jets, and other components. The part was needed to make the fast sub quieter. For decades, attack submarines had reputations for being either fast or quiet, but never both. Fast subs could be heard by adversaries who were considerable distances away. The Seawolf task needed specific expertise and scheduling requirements, as well as advanced materials and technologies.
Making connections
“Through a connection at ORNL (Oak Ridge National Laboratory), the Navy found out about us,” said Y-12 Uranium Transformation Director John Gertsen, who was part of the propulsor team. “The Navy had to find the right kind of shop for extensive and complex machining and fabrication. ORNL said, ‘We can introduce you to Y-12.’”
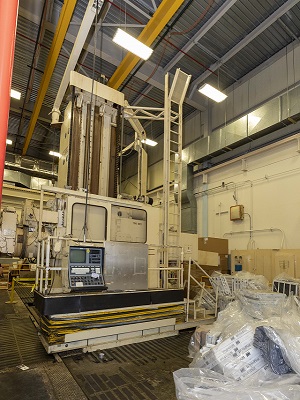
This five-axis mill has been dismantled at Alpha-1. The machine was instrumental in the production of a propulsor for the first Seawolf submarine.
The Navy explored other possible contractors, but “they knew we were capable of doing it,” Gertsen said. “Other vendors couldn’t do it, wouldn’t do it, or they wanted the Navy to build a new factory for it. The Navy came back to us.” Y-12 began work on the propulsor in 1990.
Although Y-12 had most of the equipment to build the part, the plant still needed additional machinery. This included a special five-axis, computer-controlled milling machine and a lathe. The milling machine was used to create complex shapes for the propulsor, while the lathe fashioned rings for the propulsor.
“We were given DX (a rating assigned to programs of the highest national importance) priority to get the next one coming out of the factory,” Gertsen recalled. “They told the other customer, ‘Yours is going to be late.’”
Big dismantlement with a small crew
Now, a few decades later, the mill was the focus of the recent dismantlement.
“It is a fairly small, eight-person crew that has been working on it,” said Ross Sampson, production support manager at Alpha-1, which was command central for the Seawolf propulsor project. “I’ve been involved in some other dismantlements, but nothing of this capacity.” The $2.3 million endeavor began in early September 2022.
“Despite the size of the machine, we were able to efficiently remove it,” Sampson said. “We had a high-capacity overhead crane and an experienced demolition crew. We were very strategic about how we dismantled this machine, in order to do it safely.”
The milling machine occupied a 5,000 square foot space.
“That is really just a drop in the bucket in terms of space,” Sampson said. “Alpha-1 as a whole is 278,000 square feet. But that is very valuable space.” The mill’s former space has been spoken for and will hold equipment used for special processes.
Massive equipment
The impressive 26-foot vertical turning machine was brought in as the centerpiece of the Alpha-1W wing, which was specifically added for the propulsor project. The lathe was bought used and shipped on a barge from Chattanooga.
“We needed this lathe,” Gertsen said. “It had to be big enough to do the machining on a 20-foot diameter part.” The massive lathe remains.
At one time, an area was dedicated to a large coordinate measuring machine, also purchased for the Seawolf project.
“That was a probe instead of a cutting tool,” Gertsen explained. “You probed the part to measure the surface and specific shapes. Certain shapes were important when it came to noise generation.” Sampson said that machine was removed from Alpha-1 a decade or so ago.
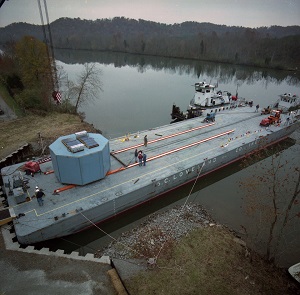
The propulsor was delivered in three subassemblies to submarine-maker General Dynamics in Connecticut, two via waterway. One of the pieces shown here is being loaded onto a barge in 1993..
In 1993, Y-12 completed the propulsor on schedule and within budget. It was divided into three subassemblies and delivered to General Dynamics in Connecticut, which built the Seawolf submarine. One part went by road in an oversize truck, and the other two made the trip via barge, starting from Oak Ridge and using the Tennessee River system. The Seawolf sub was commissioned in 1997.
Y-12 also did the model work and manufacturing design for the test propulsor for the Navy’s Virginia class submarine, made the third subassembly for the second Seawolf class submarine, crafted spare parts for the propulsors, and then transferred the process to a Navy shipyard.
Good for Y-12, the country
Although some of the machines used to help make Seawolf a stealthy vessel are no longer part of Alpha-1, the memories of that time will always ring loud for Gertsen.
“It was kind of like ‘The Hunt for Red October,’ except in that case it was the Soviets coming out with the quiet submarine,” he said. “The project gave us a real sense of accomplishment. People were proud to work on it. It showed us we can do things that are good for us [Y-12] and good for the country.”