Y-12 Blog
Installation Dog was a Y‑12 uranium storage facility from May 1948 to May 1949 that was disguised as a silo (shown above) and a barn. The area later became known as Katy’s Kitchen and now is part of the Oak Ridge National Laboratory.
In the article below, writer Amy A. shares details about working on a 2004 Y‑12 cookbook.
As a Y‑12 employee, I’ve experienced a number of blessings in my 30‑plus years, but one of the most memorable happened in 2004 while working on Katy’s Kitchen: Y‑12 Secret Recipes. This cookbook was funded by Y‑12’s managing and operating contractor with proceeds going to Y‑12’s United Way Campaign.
The title for the cookbook came from a former Y‑12 storage facility used from May 1948 to May 1949. First known by the code name “Installation Dog,” and designated as Building 9214, the original purpose of the facility, which was located on the Oak Ridge National Laboratory (ORNL) site, was to house enriched uranium after World War II.
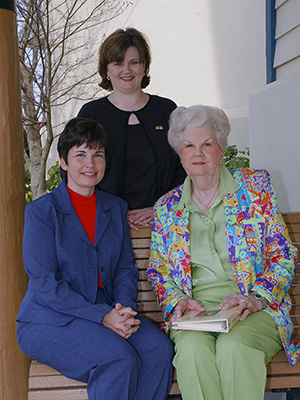
Y‑12ers Elaine W. (left) and Amy A. (center) met Kathryn Odom Howard in April 2005 to share the Katy’s Kitchen: Y‑12 Secret Recipes cookbook.
History buffs Mick Wiest and Ray Smith, both Y‑12 employees at the time, had shared with me how the secure building came to be built by Luther Agee. According to the historians, Agee never knew how or why he was chosen to design the structure, but he was told Installation Dog would be a secure building and would store bomb‑grade uranium. When built, Installation Dog was disguised as a barn and silo to camouflage it in East Tennessee’s rural farming landscape. Before completion of Installation Dog, Building 9213, an uncamouflaged facility located on the Y‑12 site, was used for storing the uranium.
In my research, I learned how Installation Dog was renamed Katy’s Kitchen after Kathryn Odom Howard in the late 1950s. During Howard’s time at X‑10 (what ORNL was referred to then), the three Oak Ridge sites (K‑25, X‑10, and Y‑12) were under one contractor. Her organization, Analytical Chemistry, was located there, and Howard often had lunch there. The group decided to nickname the facility “Katy’s Kitchen,” and the name stuck.
Working on the cookbook gave me a behind‑the‑scenes look at Y‑12’s history, offered the opportunity to work with a great crew of people, and allowed me to meet the namesake of Katy’s Kitchen.
After the cookbook was published in 2004, someone connected me with “Miss Katy.” Wiest (who worked with Y‑12 Environment, Safety, and Health then) took Miss Katy on a tour of her old work location.
“It looks so different. It brings back memories … some very good ones,” she said in an interview after the tour. Wiest coordinated the tour with an ORNL employee who said he was glad to meet the namesake of his workplace and told Miss Katy, “I thought you were a myth!” (Before coming to Y‑12, I worked at ORNL for 10 years and had never heard of Katy’s Kitchen.) Miss Katy became a friend to me and attended my wedding in 2006.
While Miss Katy didn’t have a direct Y‑12 tie, she indirectly did through the renaming of a facility. In mid‑April, I found out her great, great nephew, Griffin W., works at Y‑12. He shared his aunt passed away earlier in the month and knew Miss Katy had many ties to the Oak Ridge Reservation.
Witt said, “Even at 100 years old, she would sit with me and tell me stories for hours about working out there and how much it meant to her that I too was working in Oak Ridge — supporting the mission as she once did.”
Mick Wiest and Kathryn Odom Howard visit Katy’s Kitchen in August 2005.
Little did I know when I took on a United Way Campaign project I would experience Y‑12 history with three greats, Wiest (who passed away in 2024), Smith, and Howard.
As Smith said to me in 2004, “We can be proud of the heritage of our Y‑12 history and one of the many interesting stories associated with structures that were part of the tremendous Manhattan Project that helped win both World War II and the Cold War!”
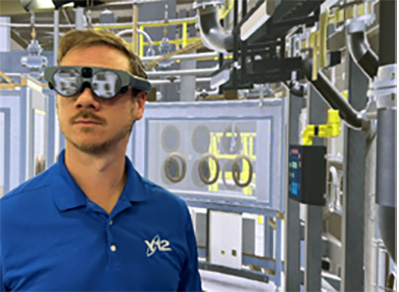
The Y‑12 National Security Complex places trainees in fully immersive virtual environments with next‑generation technologies.
It was a crazy idea, inviting the world’s best Gran Turismo gamers to get in the driver’s seat of a 600-hp Nissan GT3 to become professional race car drivers. So crazy that it actually worked. It worked because Sony’s Gran Turismo acted as extended reality (XR), a simulator that honed in the gamers’ driving skills at high speeds.
Born to be a premier facility for training in emergency response, nuclear security, and advanced technologies, the Y‑12 National Security Complex’s Oak Ridge Enhanced Technology and Training Center (ORETTC) uses XR in a similar way to train in scenarios that would be dangerous if done in the real world.
The Emergency Response Training Facility on the ORETTC campus not only focuses on training first responders but also on training Y‑12 operators on low‑occurrence, high‑consequence scenarios by using next‑generation technology, such as augmented reality, virtual reality, mixed reality (MR), and haptic feedback gloves. Funded by the Plant Directed Research, Development, and Demonstration (PDRD) program, these XR training simulations are best‑in‑class and act to fully immerse the trainee into a virtual environment through the use of these next‑gen technologies coupled with high‑fidelity digital twins developed in simulation engines such as Unreal Engine and Unity. These simulations are identical to real‑world physical spaces, persons, processes, systems, and products.
“Advances in XR have already changed the way we work, live, and play, and it’s just getting started,” PDRD Program Manager Mark Richey said. “XR literally takes ‘hands‑on’ to a whole new level. We are excited to be part of such research.”
Digital Twins and Internet of Things
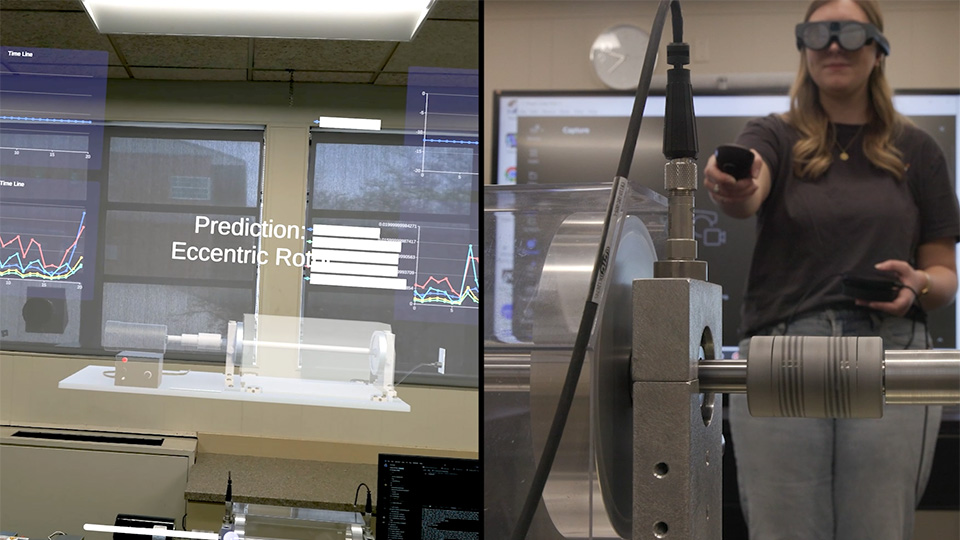
A University of Tennessee student operates a motor remotely through an XR headset and hand controllers while collecting data about the motor’s functionality.
ORETTC has unlocked Internet of Things capabilities in highly secured environments by developing a complex system engineering ecosystem that enables virtual XR headsets to access and retrieve data from real devices in a separate location. “We are able to remotely operate a motor,” said Mary Lin, interim director of ORETTC. “We can be here at ORETTC and turn on that motor at our partner facility at the University of Tennessee, Knoxville, to gain pertinent data. It’s pretty exciting.”
“The purpose of the Digital Twins and Internet of Things project is to send virtual commands to a device and also be able to read live data from a physical device as it runs,” explained Austin Arnwine, instructional technology lead. “This information loop will enable us to predict maintenance needs on machinery before it requires maintenance and even send the responsible operator the most up to date training needed to fix the machine before it needs it.”
“Y‑12 is developing digital twins at various scales,” said Scott Couture, senior director, Production Research, Development, and Integration, adding that the investment also helps create tools for other projects. “Digital twins are tools. They are a simulation at some level to help you solve a problem, such as improving the capacity and reliability of a machine.”
ORETTC applies new technology and science in a very short time frame with the goal of obtaining end products so when XR technology or machine learning advances to the next level, the technology can be integrated quickly.
“It’s so exciting! We’re not just doing the technology and science but also the application of that technology in a very short time frame,” added Tom Berg, joint adjunct assistant professor at the University of Tennessee, Knoxville. “We want to take this XR technology and machine learning to produce end products and reduce it in practice. It has so many applications outside of Y‑12!”
Collaborative XR
In the workforce today, XR is being used in many ways to collaborate with people in person and at a distance. A great example is a surgeon on the east coast who can consult with a peer/surgeon on the west coast using a secured network. This XR technology enables the ability to operate or work with a patient and meet their needs in real time while another professional is on the line.
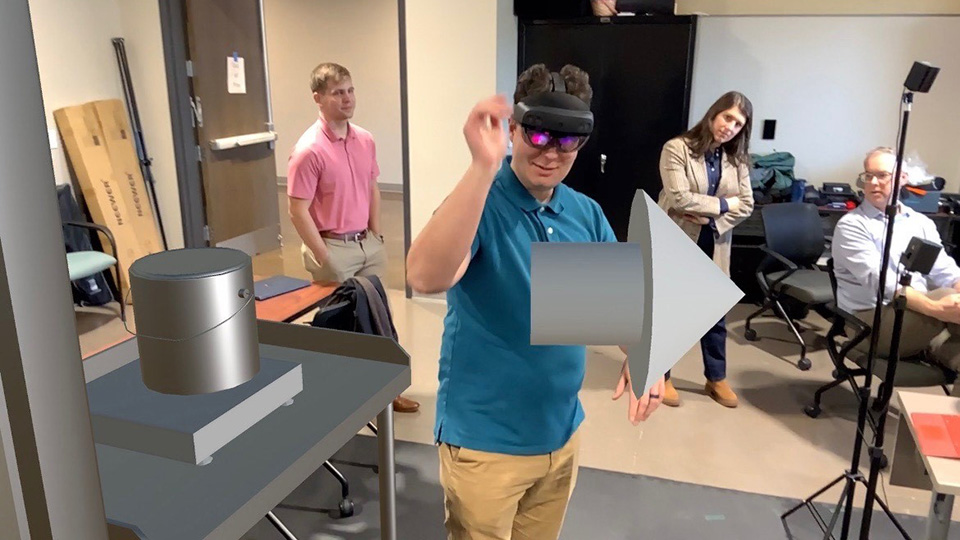
An operator is showing virtual additive manufacturing capability in a collaborative XR environment.
“The Collaborative XR project is about humanizing digital data,” explained Erik Nykwest, Y‑12 Development multi‑physics scientist. “You can set your digital asset on the table side by side with your real‑world product and compare them. You can pick up data with your hands and literally stick your head inside of it, exploring it in ways you would have never dreamed of with a two‑dimensional computer monitor. XR is an enabler that allows people to interact with digital objects as if they were real, and the collaborative aspect enhances communication and clarity when discussing complex topics.”
ORETTC has enabled this capability for additive manufacturing through funding from PDRD. Using a collaborative XR platform, ORETTC can now use headsets, tablets, and computers to convert traditional computer‑aided design (CAD) and computed tomography (CT) scans into 3‑D visuals for manufacturing and production team collaboration. This capability enables the ability to troubleshoot operations efficiently and to make design decisions without any interruption on the shop floor. These collaborations and consultations can be done in person and at a distance, as ORETTC can ship headsets to other Nuclear Security Enterprise sites for end users to collaborate as if they are in the same room.
“This technology is an evolution of how people work together moving forward,” said Arnwine. “Collaborative XR will facilitate real‑time improvements in processes and products without the need of building complex physical test models or travel for in‑person meetings.”
“For a designer or technician to be able to see what’s happening with a product or system without being in the same room is a game changer,” said Derick Weis, assistant PDRD program manager. “These platforms will facilitate real‑time improvements in processes and products.”
Haptic Feedback in Mixed Reality Glovebox Training
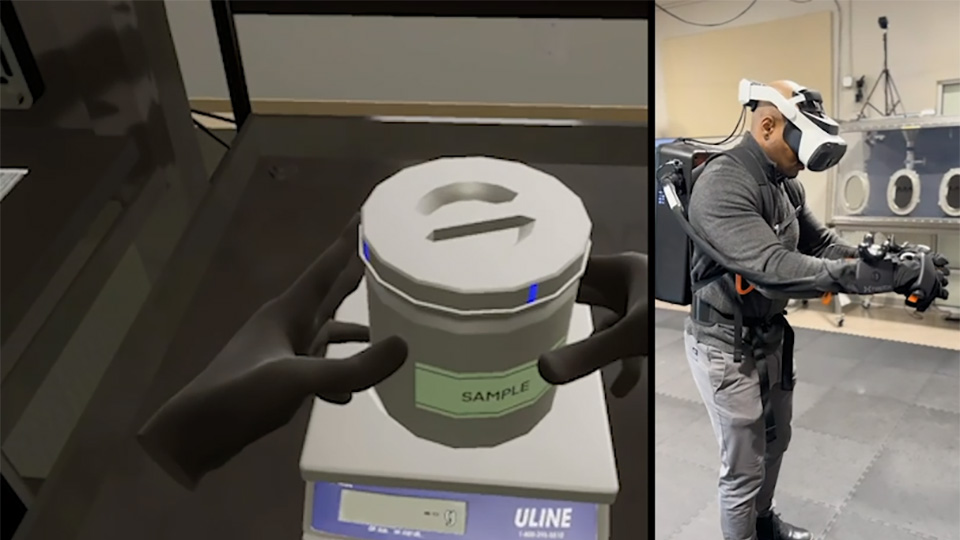
Using haptic feedback, a Y‑12 trainee works virtually to gain an understanding of the parameters of working within a glovebox.
The sense of touch and its subsequent feedback is a natural sensation often missing in XR experiences. Due to the nature of the U.S. Department of Energy’s manufacturing, dealing with sensitive materials through gloveboxes is highly touch‑driven. These glovebox jobs can be very high consequence, depending on the materials handled. ORETTC has spent the past 3 years perfecting a simulation that enables the sensations of force and texture feedback in the hands of end users in an XR training experience.
“Through the multi‑sensory engagement (touch, pressure, texture, and resistance) offered by the haptic feedback glove, chemical operator trainees feel immersed in real‑life situations while practicing conduct of operations, following procedures, and learning how to handle unlikely, but high‑stress, critical situations,” said Kim Nickell, Production Activities Training manager. “Trainees have the opportunity to practice high‑risk scenarios without real‑world consequences. Trainers are able to work with participants until the desired outcome is achieved, all while providing immediate feedback on decisions and actions that are made.”
This training experience uses haptic feedback gloves, an MR headset that the U.S. Department of Defense commonly uses for flight simulators, and a physical glovebox to simulate a material sorting exercise for new glovebox operators. This training is now being considered for placement in the Y‑12 training pipeline, as it has been tested and approved by the Y‑12 Training group and their leadership. This work was also published in “Frontiers in Virtual Reality” in March 2025 (Frontiers | VR haptics for glovebox operations training).
“With haptics in our training arsenal, trainees are getting an instructional experience that feels real,” said Weis. “It’s getting the trainees up to speed faster than traditional training methods.”
“It has been a privilege for our Production Activities Training team to work with ORETTC in the development of the Haptic Feedback Glovebox Training,” stated Nickell. “We are excited to see the future of training at Y‑12 as we adopt cutting‑edge technologies.”
Advancing XR Research and Development
“PDRD is honored to support ORETTC’s commitment to researching and developing new XR technologies and how those technologies could directly advance the manufacturing industry and NNSA’s core mission,” concluded Richey. “Through exploration of cutting‑edge solutions in immersive digital twins, haptic feedback systems, collaborative XR, and next‑generation XR environments, Y‑12’s ORETTC is driving innovation and addressing real operational needs.”
These advancements enhance workforce readiness, improve safety, increase precision, and streamline complex processes. Through strategic partnerships and forward‑thinking research, Y‑12 lays the groundwork for a more agile, capable, and future‑ready manufacturing ecosystem. Our efforts ensure that we remain at the forefront of technological progress, shaping the industry and setting new standards for excellence.
Terra M. is a night shift carpenter on the UPF Project and is one of many traveling craft professionals working at the site.
The road less traveled has proven to be a path to leadership for Terra M.
Terra is a night shift carpenter on the UPF Project and is one of many traveling craft professionals working on the site. In construction for 18 years, her career began in Alabama when her brother‑in‑law introduced her to the local union.
“I needed a job that would help support my family, and he took me right down to the union hall. I was immediately hired. I didn’t know anything, but I spent 4 years as a union apprentice and they taught me everything,” she said.
Once she was trained as a carpenter, she left Alabama and began traveling the country honing her craft. From Pennsylvania to Minnesota, Terra worked at nine different sites before joining the UPF Project in 2022. At UPF, she was invited to participate in the Craft Based Leadership (CBL) program, where she discovered herself on a new and different road.
“I’ve never worked in a place that is so supportive and treats me so well,” she said.
Since joining the CBL team, Terra has found a love of teaching. She said the CBL program allows her to coach in every craft, and she finds a way to connect with everyone.
“I always start the conversation by asking how someone is doing. I want to make sure that they aren’t carrying something into work that could become a safety issue. I care about each person,” she said.
Her motivating factor is helping people, and she takes pride in carrying the responsibility of leadership.
“I’m the leader of my family, and I feel the same way about the people I work with. They are my family, and I try to encourage them every day,” she said, noting that she has three ‘E’s for leadership. “I want to engage, encourage, and excel with everyone I talk to. It is important to me that everyone leaves the job site healthy and whole.”
In a competitive construction field, Terra has faced her fair share of challenges, but she keeps a good perspective.
“Being in this field can be rough,” she said. “You have your ups and downs, especially when you are trying to figure out what you are good at. You have to weather the storm, and, after 18 years, I have finally weathered that storm. UPF is the best place I’ve worked.”
Terra’s perspective and talent has made an impression on her managers and site leadership.
“She is the model for what we look for in CBL members," said Night Shift Environmental, Safety, and Health Lead Redd J.. “She is dedicated, knowledgeable, has a field presence, and is a great communicator. Terra is a courageous leader, who always has a great attitude. She is consistent and intent on absorbing as much knowledge and understanding as she can and upholds the standards of safety. For her, not even the sky is the limit.”
“Terra has become an integral part of our Night Shift Construction team,” added Sam B., Night Shift Construction manager. “She works tirelessly to coach our evolving and growing workforce, takes the lead in our Craft Based Leadership team, and supports a highly successful and safe night shift ES&H program.”
She goes home every month or so to her family and to her community, where she hopes to inspire others to take the road less traveled. One of her proudest moments came when her nine‑year‑old niece was in a pageant; when the panel asked Terra’s niece what she wanted to be when she grew up, she said she wanted to be “a carpenter like my auntie.”
Terra said her advice to those who are considering going into construction is to take time to explore.
“Find things out for yourself. Don’t let others determine what you want in life. The road is tough, so stay focused, stay encouraged, and don’t give up. Remember, every place isn’t for everybody, so don’t let someone discourage you from going somewhere new, just because they said so. Find out for yourself.”
Will (left) and Ed R..(right) showcase the plaques they received for their joint patent, “Method of Making an Annular Radioisotope Target Having a Helical Coil-Shaped Foil Ribbon Between Cladding Tubes.”
As an engineer and researcher for more than 35 years at Y‑12, Ed R. has held many roles. He certainly understands the importance of continuous improvement through constant evaluation, research, and development of new processes and technologies. Working with the Technology Transfer Office, he has spearheaded and received 34 patents stemming from his work.
His most recent patent, though, just might be his favorite.
Forming a father‑son team
Ed’s son, Will, had just started working as a systems engineer in Y‑12 Development at the time Ed had begun working on a project related to annular, or tube‑shaped, radioisotopes. While Will was waiting on his security clearance, Ed thought this project would be a great opportunity for Will to gain experience and learn about Development.
“When this idea came to mind, I jumped at the chance,” said Ed. “It was an opportunity for us to work together on something, while also providing Will with important experience and education.”
They quickly set up a process to work together on the project and met daily.
“Getting the chance to work with my dad on this project was really cool,” said Will, now shift technical advisor. “Having just transferred to Y‑12 and waiting on my clearance, it was an amazing opportunity to do work on new technology while I was working on my prerequisites as a systems engineer.”
Developing a new and improved technology
Process improvement is crucial to the Y‑12 mission, especially when an improved process can save time and increase worker safety. The duo established those goals when they began working on a new method for the annular radioisotope assembly process.
The previous method uses a flat foil that is wrapped into a C‑shape around an inner tubing. The foil then has an outer tube slid over it, and the ends are welded shut to prevent foil movement. The process concludes by expanding the inner and outer tubes to obtain a final desired dimension. This method can cause quality issues with the final product and can increase worker exposure times due to potential buckling of the foil.
“We were able to take an in‑depth look at this labor‑intensive process and then find ways to improve it,” Ed said.
Working together daily, Ed and Will developed an improved and more efficient technology and method. The new method simply cuts the foil that wraps around the inner tube into a helical coil or spring. The helical coil can be twisted to tightly grip the inner tubing with edges on the foil that lock together when tightened. Conducting the process through this new and improved technology prevents gaps and overlaps of the foil that would otherwise hurt the quality of the final product. The helical design speeds up the overall process by eliminating the potential for buckling of the foil, which reduces exposure time to employees.
“This technology brings the ability to create medical isotopes in a repeatable and effective way with an extremely high percentage of usable material and minimal waste,” Will said. “It brings a ton of potential to both the NSE [Nuclear Security Enterprise] and the medical industry.”
Receiving a patent
As the development of this new technology and method were coming to a close, Ed began showing Will how to conduct patent searches to ensure their method was unique and how to ensure it was protected through the Y‑12 Technology Transfer Office.
“Having no experience with the patent process at Y‑12, I was very impressed with how streamlined and simple the process is,” said Will. “The Tech Transfer group knows how to get the ball rolling and help guide you through everything.”
Once it was confirmed that their approach was completely new, they proceeded with filing a patent through the Technology Transfer Office. This patent was Will’s first, and working as a father‑son team made the success that much better.
“I loved every second of it,” Ed said. “Your first patent is truly a milestone, and I have so much pride for Will and how big of an accomplishment this was for him. It’s always great to see your kid succeed, but being able to work together in the process of it all made it so much more meaningful.”
Will said, “I had wanted to work at Y‑12 since I was a little kid. Having grown up hearing about all of the cool projects my dad had been part of, it was extremely special to finally be part of one.”
The new Y‑12 technology can be useful within the NSE, but it has potential to have a large impact within the medical industry as well. Hospitals worldwide use radioisotopes in medicine and for diagnostic scan procedures. Y‑12’s technology is applicable to all isotope productions, so there is potential to commercialize this technology to other industries.
“At Y‑12, we get to go beyond the leading edge of technology,” said Ed. “I’m grateful we get to develop things that people will be using and reading about for decades to come.”
In his short time in East Tennessee, Tyler M. has already experienced the intense fan noise in Neyland Stadium and enjoyed the serenity of the Smoky Mountains. Now his objective is ensuring Y‑12 employees complete FY 2025 Stockpile Programs mission work.
When “UT” is mentioned in East Tennessee, the default assumption is in reference to the University of Tennessee. This implication is new for the senior director of Stockpile Programs, Tyler M. As an Amarillo native, his first thought is the University of Texas, but he is slowly adapting to equating “UT” to the “University of Tennessee.” It helps his fiancée is a UT (yes, Tennessee) graduate.
Tyler, a Pantexan for 13 years, joined Y‑12 in November 2024. He replaced Reed Mullins, the current vice president of Mission Execution. Tyler is excited to be on the East Tennessee side of the Nuclear Security Enterprise mission, surrounded by mountains and rivers. “I love having the opportunity to learn about Y‑12’s production capabilities and material streams. At Pantex, we received Y‑12’s finished product. It is enlightening to witness the complexity of manufacturing the mission deliverables.”
Tyler realizes there will be challenges ahead as Y‑12 adapts to the growing workload. “Stockpile Programs is responsible for the strategic planning of scope, schedule, and cost associated with weapon deliverables at Y‑12. We recognize the demand will continue to increase and require a more agile and efficient approach to mission execution,” he said. “I am fortunate to have a strong and knowledgeable team capable of this critical endeavor.”
Tyler, who has a B.S. in mechanical engineering and an M.S. and Ph.D. in systems and engineering management, started his career as a tool design engineer at Pantex. He graduated from the Sandia National Laboratories Weapon Intern Program in 2017, during which time he visited Y‑12 for the first time. After his WIP graduation, Tyler worked as the manager responsible for the weapon programs’ safety basis. Following this role, he was a weapon program manager and observed the star stamp of the first production unit. In 2022, he was selected to be the senior technical advisor for production for NA‑122, also known as the Office of Stockpile Sustainment, at the National Nuclear Security Administration Headquarters in Washington, D.C.
As a former West Texas A&M University baseball player, Tyler understands the importance of teamwork and recognizes it as the most impactful CNS value. “Teamwork is required to successfully execute our mission. The three additional CNS values of trust, integrity, and respect provide a strong foundation for teamwork.”
Tyler is ready to support the mission in his new role and said, “It takes the whole site to make Y‑12 successful. Let’s continue addressing FY 2025 milestones and have a successful year.”