Y-12 advances technology for assessing fire systems
Guided wave ultrasonic testing involves wrapping an ultrasonic, low-frequency transducer ring around a pipe and sending a pulse 100 feet in both directions to test for pipe obstructions and pipe-wall thickness.
A project to deliver a new technology for assessing Y-12 fire suppression systems is on track for completion in 2021. Five employees qualified with the equipment earlier this year, and the technology is now in the proof-of-concept phase.
The project involves using a nondestructive tool—guided wave ultrasonic testing (GWUT)—to screen wet and dry fire suppression systems for blockages or corrosion. Use of nondestructive technology for assessment is important because many of the pipes in the fire suppression systems were installed about 70 years ago, and the current testing method Y-12 uses requires the removal of piping sections.
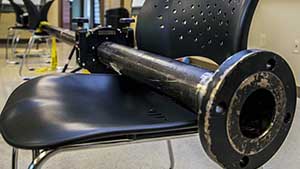
The 9-foot test rig completed by the metal fabrication shop for the training on guided wave ultrasonic testing.
“There is a risk in dealing with old pipe,” said Bobby Jenkins, Emergency Services Systems Operations manager, who initiated pursuing a nondestructive assessment method. “The nondestructive method is better in terms of risk and cost. We don’t need to disassemble pipe or take out sections unless we find something.”
Jenkins’ interest in nondestructive assessment led him to Steve Dekanich, a senior metallurgist in Quality Operations Support. “We needed a way to streamline the process and make it more efficient and cost effective,” Dekanich said.
He explained the GWUT method can test a 200 foot section of pipe at one time, whereas the existing method can only test a 10-foot section. GWUT involves wrapping an ultrasonic, low-frequency transducer collar around a pipe and sending a pulse 100 feet in both directions to test for pipe obstructions and pipe-wall thickness.
During proof-of-concept testing, the equipment will be placed in a central location where the researchers and newly qualified equipment operators will work on technical development using sample piping.
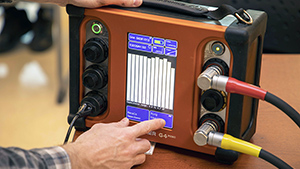
The Wavemaker G4 Mini from Guided Ultrasonics Ltd. connects to the transducer rings and collects guided wave ultrasonic testing data for further analysis.
“This new method is a lower-cost activity. We can cover a lot more area with new equipment. This method is smarter, more efficient,” Jenkins said. Y-12 maintains nearly 300 sprinkler systems and performs 15 to 20 internal inspections each year at an annual cost of $200,000.
Both Dekanich and Project and training lead Aaron Bales see the GWUT method as having potential for implementation across the Nuclear Security Enterprise because of its efficiency and costs savings.
Most importantly, Jenkins said, “This tool provides assurance of reliability in the event the system needs to be used. It’s one less thing to worry about.”