Y-12 Apprenticeship Program prepares future trades workers
For more than 10 years, the Y-12 Apprenticeship Program has been in business, training employees for professions in trades like pipefitters, electricians, machinists, and ironworkers. The program, restarted in 2008 as a cost savings proposal, allows hands-on training for key positions within the site.
Will Farmer of Y-12 Infrastructure said, “We’re at a junction where a significant percentage of the skilled craft personnel supporting vital activities are retirement-eligible or will be retirement-eligible within the next five years. The Apprenticeship Program allows us to address this issue by developing a strategic staffing approach that focuses on attrition projections.”
Apprentice graduate and now apprentice supervisor Zach Yost said, “The program is important to CNS and Y-12 because there is a need for skilled craft workers in our current and future mission scope. The apprentices won’t just learn the skills to become a Department of Labor–recognized journey worker; they will also be uniquely qualified to perform their skilled trade within the compliance-driven environment of Y-12.”
Infrastructure works with the Atomic Trades and Labor Council, Production, and Human Resources to develop a five-year look-ahead staffing plan to meet the resource demand in critical-skill craft positions.
“Currently, we have 21 apprentices in three types of apprenticeships that range from three years to five years,” Farmer said. “Our partnership with the ATLC provides selected candidates the opportunity to learn a skill trade through classroom learning and hands-on experience with Y-12–specific equipment, systems, and processes that support our country’s national security initiatives. Through the program, we’re enabling personal growth for the candidates while ensuring continued Y-12 mission success now and for the future.”
Chris Drinnon, a fifth-year pipefitter apprentice who will finish in September, recommends the program. “With the rising cost of college tuition, apprenticeship programs are a great alternative. Plus, America is experiencing a major shortage of qualified trade workers, and apprenticeship programs are a solution to this ongoing problem.”
During 2019, Y-12 began educating tomorrow’s workforce about the opportunities available in trades by holding educational outreach events that focus on the various trades careers available. At the events, students interact with electricians, carpenters, insulators, painters, and machinists. ATLC members share career plans and the advantages of being an apprentice and “earning while they learn.”
Katie Mead is a first-year apprentice as an outside machinist and agrees with Drinnon. “It is a great opportunity to further your education, learn a new skill or trade, and avoid having the large amount of student loans that come with traditional schooling.”
Drinnon said, “Aside from apprenticeship classwork, gaining knowledge out in the field of building processes and systems has been vital. Currently, apprentices work three-month rotations in different workshops throughout Y-12. By doing this, it allows each apprentice to gain valuable knowledge in multiple areas.”
“Hands-on training, company training programs, Red Vector training modules, and school offer a wide range of educational tools and information,” Mead said. “By combining all of the knowledge obtained in these programs, I feel like that is what is helping to mold me into being the best outside machinist I can be.”
As most of us know, reaching a goal often takes a little stretching to accomplish it, and being an apprentice is no different.
“The hardest part for me has been the late nights getting home from class. For nine months a year and two times a week, 18-hour days are tough, especially as a 48-year-old with a family,” Drinnon said.
Mead expects the toughest part to be the group rotations. “You only have a short amount of time with each group, so it can be tough having to adjust each time.”
Drinnon offered advice to Mead and other new apprentices: “There will be tons of information thrown your way throughout this process. It can be overwhelming. Be patient.”
The apprentices’ dedication and experience can also help them become tomorrow’s leaders. Yost said, “Based on recent history, the individuals going through the apprenticeship are also the future leaders within Maintenance Execution and other organizations.”
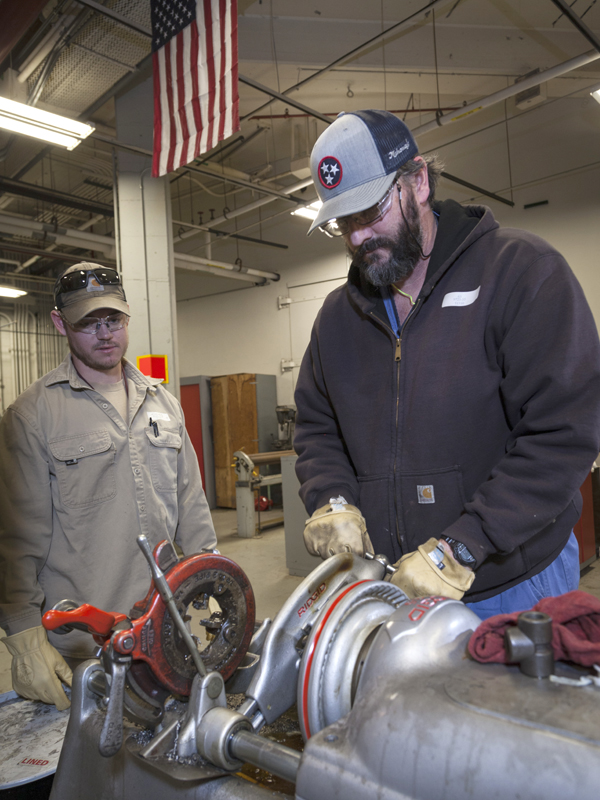
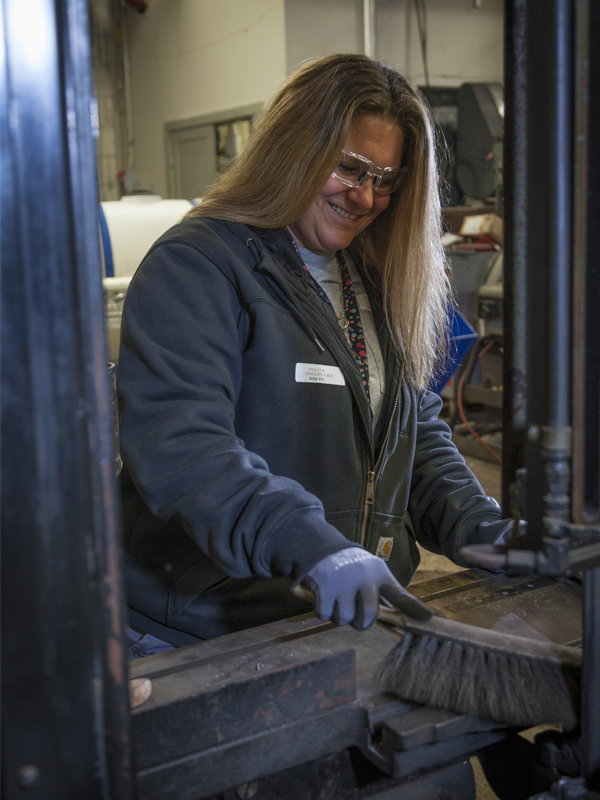
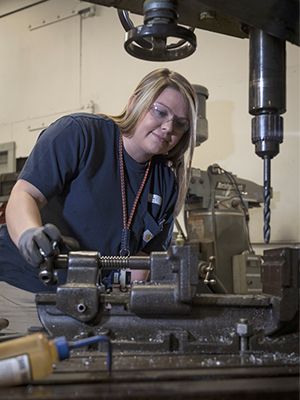
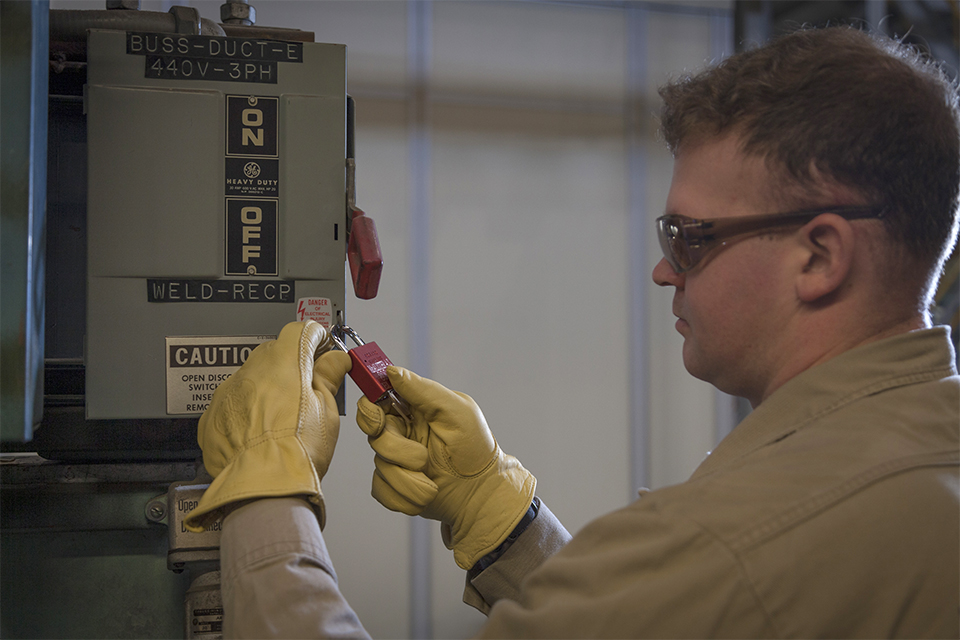
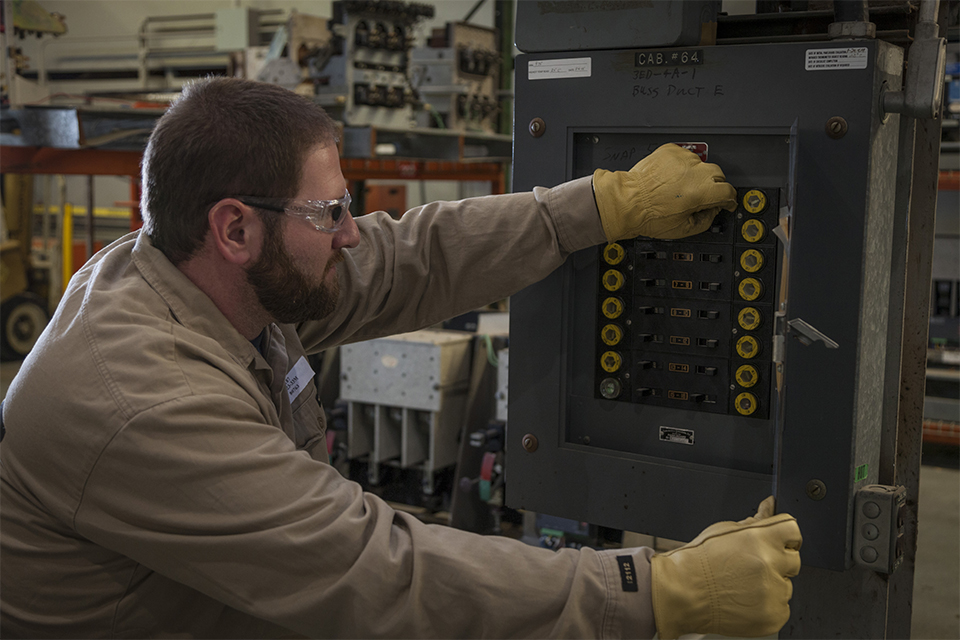
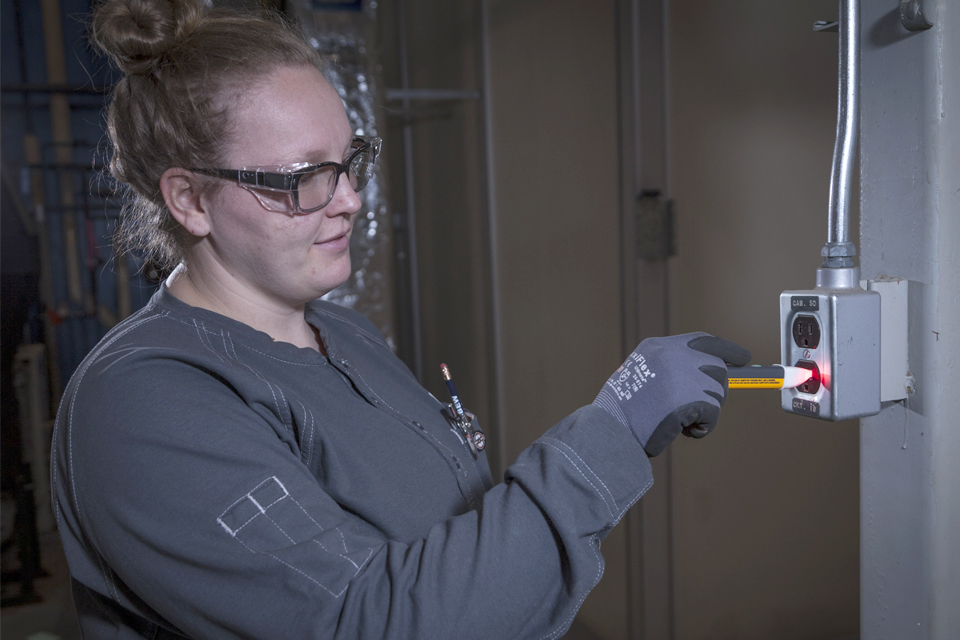