Y-12 Blog
After almost 30 years of military service and a stint at Pantex, Chris Burns is now ready to serve at Y-12. Photo by Matthew Harkins.
The Y‑12er spotlight details one of our own, Chris Burns, vice president of Safeguards, Security, and Emergency Services. It takes all Y‑12 employees to make the mission happen successfully and safely. All views and opinions are the employee’s own and do not necessarily reflect those of CNS.
Chris Burns is not new to Consolidated Nuclear Security. He was the senior director of Safeguards and Security at the Pantex Plant and has now moved from Texas to Tennessee to serve as vice president of Safeguards, Security, and Emergency Services (SS&ES).
Prior to joining CNS, Burns served almost 30 years in the Army, retiring as a colonel. During his time in the military, he held various command and non‑command roles, including deputy Provost Marshal General of the U.S. Army, director of Army Inspections, commander of both the 759th Military Police Battalion and 42nd Military Police Brigade, and director of emergency services for Joint Base Lewis‑McChord.
Despite his military experience, Burns said he didn’t know anything about DOE and NNSA. However, when he was preparing to retire, David Turner (vice president of Operations Support and a fellow Army retiree) suggested he look into the work at Pantex and Y‑12.
“When I read the duty description, I got really excited,” said Burns. “The facilities are central to the security of our nation.”
Burns understands that employees interacting with SS&ES may not be having their best day. #&8220;As a whole, we have to be at our best when we come to work every day; so, we’ll be at our best when you may be at your worst.”
What excites you about your new role?
I am most excited to have the opportunity to help shape the future of Y‑12. The site is evolving, and Safeguards, Security, and Emergency Services (SS&ES) has to evolve as well. Change is hard for most, but working with true professionals here at Y‑12, especially in SS&ES, makes change a bit easier to swallow.
Share your history prior to joining CNS.
I served in the military for almost 30 years, with multiple combat tours between Iraq and Afghanistan, not to mention a few other places, but my transition out of uniform and into civilian life was well supported by both the Army and CNS. My first 14 months as a civilian were spent as the senior director of Safeguards and Security at the Pantex Plant. It was a tremendous opportunity, and I learned a lot about the company, NNSA., and the DOE. For me, the mission and the people were a good fit!
What knowledge/history do you have of Y‑12?
When I was transitioning out of the military, I didn’t know anything about DOE/NNSA. What I did know was a bit about the Manhattan Project, but I didn’t know a piece of that history resided right here at Y‑12.
What top strength do you bring to your organization and why?
I think I bring calmness, along with a fresh set of eyes. I don’t get overly excited, which is a skill set I bring from the U.S. Army. You have to be that calm voice in the midst of crisis or problem‑solving. Having a fresh set of eyes allows me to see things from a different angle and allows me to provide potential solutions or recommendations that aren’t limited or constrained from being in the environment for an extended period of time.
What role do communications play in your job?
Communications play a critical role in how we communicate security changes or critical events. Often, people don’t want SS&ES around until they need us. Why? Because we are inconvenience and delays. We want to move from that reactive response model to a more proactive one that requires us to be a teach-and-train organization. That type of organization requires strong communications. We also want to interface better with our teammates and build more depth to our security programs. For example, take the division security officer program. The Y‑12 Division Security Officer (DSO) program is designed to ensure Safeguards and Security (with an emphasis on Information Security) is intricately entwined with each Y‑12 organization and its operational needs through a centralized representative or group of representatives. These organizational DSOs, in essence, become an extension of Safeguards and Security by providing each organization a conduit through which security needs, awareness, challenges, and overall compliance can be funneled. Their importance, if used correctly, can be widespread and provide a huge impact to each organization, security, and site mission deliverables/challenges.
Why is teamwork an important aspect when working at Y‑12?
There’s no “I” in team. Teamwork is the essence or cornerstone of any organization. All leaders are responsible for building their team. Effective teamwork requires collaboration, communication, trust, and respect. It also emphasizes the importance of shared commitment and diverse perspectives.
Why is it important that we hold ourselves accountable in our daily tasks?
If we’re not accountable, nothing gets done. Accountability is one of 16 traits that a leader must possess in order to be successful. Most folks are self‑critical and recognize that we are responsible for what does or does not happen in our daily tasks. Accountability allows you to take responsibility for your own actions and decisions, and it builds trust with the people around you. It’s easy to see the benefits of personal accountability. Whether you’re the CEO or just starting an entry‑level position, your team members will know that you’re reliable and can be counted on.
What advice would you give a newer employee about the importance of solving problems and asking questions?
When it comes to solving problems, it is important to make sure you define what the problem actually is before you try to solve it. You can waste a lot of energy when the problem is not properly defined, so make sure you’re focusing on the right problem.
It’s also important to listen and ask questions. A good leader can guide a team by asking the right questions at the right time. There’s definitely an art and a science to it.
What’s your top bucket list item and why?
My wife and I want to visit every NFL and MLB stadium. We’re both sports fans, but it’s more than that — it’s about making the memories.
After 20+ years at Pantex, Josh Gerken is ready to make Y-12 his work home. Photo by Joy Kimbrough.
The Y‑12er spotlight shines on one of our own, Josh Gerken, the vice president of Program Integration. It takes all Y‑12 employees to make the mission happen successfully and safely. All views and opinions are the employee’s own and do not necessarily reflect those of CNS.
His is a name and face many Y‑12ers know from his efforts on the Pantex and Y‑12 contract transition during 2024. Now this former Pantexan is a Y‑12er. Get acquainted with Josh Gerken, vice president of Program Integration.
“Until contract transition, I was a career‑long Pantex employee,” Gerken said. “I started at the site in 2001 as a technician in the Gas Analysis Laboratory and have been extremely blessed with opportunities in both technical and leadership roles that support NNSA’s important mission.”
The decision to join Y‑12 wasn’t one Gerken made easily, as it meant leaving behind his family, his roots, and his colleagues. “I miss my Pantex group as I worked with them for 20 years, but I have no worries about developing similar bonds here. Your work relationships and network are important.”
His new role does reach back to the Pantex network, which continues to enhance the Pantex and Y‑12 partnership. “I served as the senior director of Stockpile Programs at CNS for about 2 years until we made the smart decision to divide this role into site‑specific responsibilities,” he said. “I was able to learn a fair amount about the weapons scope at Y‑12; however, given the large size of that scope, as well as the important role that the Oak Ridge Corridor has played and continues to play in our country’s history, I realize that I have so much more to learn.”
And learning is something he does regularly. “I have had team members in the past jokingly tell me I ask too many questions, but asking questions can help me and others learn or view a situation through a new lens.”
His technical experience is an advantage in his role. “I bring a relatively strong technical background to the team, as well as a fresh set of eyes,” Gerken said. “I hope I can bring that perspective, as well as the continued relationships with the site, to Y‑12.”
Gerken sees his role at Y‑12 as a “good trade because I get to see the background and get involved earlier in the process. The pride at Y‑12 and historical legacy of the Manhattan Project that people embrace is really cool. During my time here, I’ve not met anyone who views working here as just a job.”
How can communications make (or break) a task being worked?
Often, without communication, a problem can snowball to where the solution becomes much more complicated. Communications with colleagues, leadership, and customers is vital to ensuring solutions get identified and worked at the appropriate level.
How has teamwork allowed you to grow as an employee?
It has made me realize how dependent we all are on each other, whether as a work group, a site, or an enterprise. Our mission is far too complex to depend on any sole entity. When I realized this and the aperture was opened, it amplified my pride in our mission.
How do our established procedures, administrative controls, rules, etc. help us in being accountable to CNS, our site, and our peers?
Our procedures and policies are what allow us to come to work, deliver on NNSA’s mission with high quality, and go home safely every day. Practicing disciplined operations and never settling underpin CNS’s ability to deliver on such an important mission.
What is the top lesson you have learned by applying problem‑solving skills to an issue?
Do not be afraid to ask for help. There is likely always someone that is going to know more or has more experience in an area who can help with a higher quality solution than going alone.
If you are new to the area, what is something you are looking forward to doing?
We are looking forward to becoming part of the East Tennessee community. The decision to move here was not taken lightly, as all of my family is in Texas, but this was an amazing opportunity with CNS that was too good to pass on. Personally, I have always wanted to live near the mountains, and now that I do, I suppose I should take advantage of all of the activities that the area has to offer!
Meet Jon Ragan who is a new member of the Business Management and Transformation leadership team. Photo by Jordan Ray.
Learn about Jon Ragan, the new deputy for Business Management and Transformation. It takes all Y‑12 employees to make the mission happen successfully and safely. All views and opinions are the employee’s own and do not necessarily reflect those of Consolidated Nuclear Security (CNS).
Jon Ragan joined CNS in September, and since that time, he has been driven to learn the ropes of work he calls “challenging, complex, and important.” Ragan was the vice president and deputy general manager of National Aerospace Solutions, LLC, which held the test operations and sustainment contract at the U.S. Air Force’s Arnold Engineering Development Complex (AEDC). At AEDC, he was responsible for Business Operations, which included Project Controls, Supply Chain, Information Systems and Technology, Finance, Human Resources, and Office and Administrative Services, as well as Performance Assurance, which included Safety, Quality, Training, and Continuous Improvement.
“I’m amazed at the complexity of the work that takes place at Y‑12,” Ragan said. “What stands out to me since joining the team is that many of the challenges are quite similar to what I experienced in my last job. While AEDC was smaller in scale and is not the nation’s premier national security complex, we had the same culture of mission and nation first, and similar to Y‑12, we faced challenges with aging infrastructure and tight national security timelines. I’ve also been very impressed with the high level of talent here and commitment to the mission by those I work with.”
He’s not one to stay quiet as he said, “Ask questions. Lots of questions. There is a lot to learn from everyone here.”
Ragan is the deputy for Business Management and Transformation where he oversees key business management tasks and improving processes within the organization. As a first assignment, he’s developing and implementing a digital transformation (DT) structure for Y‑12.
“We have several great working groups and many smart people executing DT‑type projects,” he said. “There is a lot going on in this space, so we need a centralized approach. With help from others, I am creating a Master Integrated Project Team that enables a prioritized and coordinated approach for DT efforts across Y‑12, one that keeps us aligned with all stakeholders and the NNSA DT efforts. This structure will provide the ability to plan and integrate project activities across the Y‑12 organizations and working groups, increase focus on priority efforts that support our requirements, improve disciplined operations and operational efficiencies, and act as an integrator for digital transformation across the site. I have been working closely with our Chief Technology Officer (CTO), and once this structure is stood up, I’ll hand the reigns to him along with the digital transformation program manager. But, because this is near and dear to my heart, I will definitely stay involved.”
During Ragan’s 19‑year career with Bechtel, he has dealt with designing and constructing launch infrastructure to destroying chemical weapons to testing weapons systems. Before he worked at AEDC, he spent 9 years in “chem‑demil” as the deputy business manager for Bechtel’s Blue Grass Chemical Agent‑Destruction Pilot Plant and assistant project manager and business manager for Bechtel’s Pueblo Chemical Agent‑Destruction Pilot Plant.
“Throughout my career, I’ve known the importance of the work we do at Y‑12, and I am very proud to now be on the ground and part of it. Now that I am a part of the team, it has reinforced my thoughts on the importance of the CNS and Y‑12 mission.”
What advice do you offer someone who has made a mistake in his or her job? How should they be accountable for that issue?
Mistakes are not necessarily bad. I like to look at them as learning opportunities; if you make a mistake, own up to it, and make sure you learn from it. When I make a mistake, I take some time to think through what went wrong and figure out how I can do better next time a similar situation arises.
What daily task lets you know you’re helping achieve the CNS mission? How/why does that task let you know you’re working toward the mission?
I see Business Management and Transformation as an enabler to the mission. If I can help to improve a process or processes by implementing change that enables our workforce to more efficiently and effectively support the mission or reduce unnecessary steps (and associated distractions) from a business process, I feel I’m working toward the mission.
What top strength do you bring to your organization and why?
I think it would be persistence and resourcefulness. I like a good challenge and I will find the right information and get the right people involved to resolve it.
Why is teamwork an important aspect when working at Y‑12?
The work here is so important and complex; it takes the best of everyone to achieve the mission. Teamwork is key. At Y‑12, we have production workers to Ph.D. scientists to accountants, to name a few. Everyone’s job is important, and everyone brings a different background and input that contribute to the success we have here.
What’s your favorite outside‑of‑work activity and why?
I enjoy spending time with my family, working on old cars, and barbequing. I have an old Jeep I like to take out on trails. While I haven’t made it to any local trails since I’ve been in the area, it’s definitely on my list.
Ensley W. is an enthusiastic go-getter who joined the UPF Project as an ironworker apprentice in June 2024 while attending Tennessee College of Applied Technology (TCAT) in Knoxville.
“I chose to go to TCAT because I wanted a better life, and welding was intriguing,” she said. “I wanted to know how to weld for artistic reasons but quickly figured out that the skill could offer me a lot more as a career.”
Raised by a single mother, Ensley said her mom worked two or three jobs to provide for her and her two siblings, and with her grandparents’ help, she was able to work a part‑time job and attend welding school at TCAT.
After posting a video on Facebook of a welding bend test that she did in a TCAT class, she was contacted by a friend who told her to check out the local union because it was hiring welders. What was intended to be a meet and greet at the local union hall turned into a job offer to work on the UPF Project.
When asked about working with her UPF Project team, she said, “It’s a lot easier to come to work when you like your coworkers. It’s like working with your brothers. They are teaching me a lot and are very helpful. This is a cool thing to be a part of — being able to build something that will keep us all safe is awesome.”
The opportunity to take advantage of this type of career path is not lost on her. With emotion in her voice, she said, “I now have the opportunity to go higher. My mom and grandparents are very proud of me because I have the option to advance my life. They are happy and excited for the path that I am on.”
Being part of the CNS craft family is important to her after her apprenticeship graduation. “I would love to stay on the project after I top out. The promotion track is incredible. They incentivize you to stay and do a good job. The opportunity to learn is all around.”
Bruce B., union steward, is pleased with Ensley’s progress.
“She is a very good apprentice. She came to us straight out of high school and is a very quick learner,” Brown said. “Apprentices are able to acquire on‑the‑job‑training and true‑life experiences that they cannot get in the classroom or from books. They learn how to deal with different situations and people. They also learn the importance of ethics, honesty, and how to achieve quality work. Training of apprentices properly is critical to the continuation of the union and the construction industry. So, I feel it is very important to have apprentices on this project — our future depends on it.”
To anyone considering a trade school as a college alternative, Ensley offers, “I would tell them to go for it. It’s 3 to 5 years of your life, and there are so many benefits to being part of the union. You can be successful if you stick with it. Having a skill like this affords people opportunities for a better life.”
She graduated from the TCAT welding program in August 2024 and will complete the apprenticeship program in April 2027. Since graduating, she has been asked by TCAT instructors to monitor and judge student bend tests. To date, there are 100 apprentices working on the UPF Project.
Daniel Riddick, Y‑12 Technology Transfer program manager, engaged with potential partners at NNSA’s Innovation Day in Arlington, VA.
The National Nuclear Security Administration (NNSA) established Innovation Day to enhance future collaborations, technology transfer, and mission‑critical capabilities. The widely attended event offered opportunities for business owners, inventors, and Nuclear Security Enterprise (NSE) labs, plants, and sites to connect on potential collaborations. Y‑12 National Security Complex was able to build new connections and further develop current ones by attendance at the forum.
“NNSA carries forward the legacy of the Manhattan Project, which represents the starting point for leveraging academia and the private sector for defense innovation,” said Jahleel Hudson, director of NNSA’s Technology and Partnerships Office. “NNSA Innovation Day brought together potential commercial partners and our NSE laboratories, plants, and sites to identify synergies that can enhance our national security and economic prosperity. We appreciate the participation of our NSE sites, such as Y‑12, who brought their expertise to Innovation Day and featured their technologies invented in the course of nuclear security mission work that can transition to commercial solutions to stimulate business growth and improve our daily lives.”
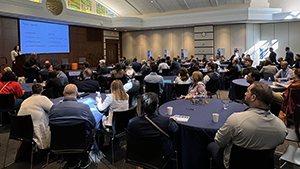
NNSA’s Innovation Day in Arlington, VA. (Photo by Grant Allard.)
Innovation Day was beneficial for Y‑12, with staff making 19 industry connections and receiving a number of inquiries on potential partnership opportunities. Y‑12 Partnerships and Technology Transfer leadership also engaged with DOE and NNSA to share Y‑12’s approach of using technology transfer for mission work, employing data analytics, and integrating technology transfer into the site’s university partnerships portfolio.
“Attending events like Innovation Day and establishing connections is crucial,” said Daniel Riddick, Y‑12 Technology Transfer program manager. “We created positive momentum and developed connections with potential partners. We’re grateful that NNSA provided us this opportunity.”
Y‑12 manages a portfolio of 148 patented technologies that are available for government and commercial licensing, 120 of which have at least 5 years before expiration. Technology transfer benefits Y‑12’s core nuclear production mission by providing opportunities to accelerate technology maturity through private industrial investment. Some of Y‑12’s technologies featured at NNSA Innovation Day include:
- The Modulated Tool‑Path (MTP) Chip‑Breaking System — a cost‑saving solution for machining operations that creates continuous chips in a significantly safer environment
- Chemical Identification by Magneto‑Elastic Sensing (ChIMES) — a new, low‑cost sensor technology developed in collaboration with the University of Tennessee, Knoxville, that uses target response materials (TRMs) as actuators in magneto‑elastic sensors
Collaborating with industry partners to mature and commercialize technology is essential to building an industrial base that supports the NSE’s labs, plants, and sites and maximizes value for the taxpayers.
If you are interested in exploring a potential collaboration with Y‑12, please email OTCP@y12nsc.doe.gov.