Y-12 Blog
Photo: YPH‑25‑1196376.jpg Subcontract Technical Representative Jamie P. shares her thoughts on teamwork as part of a series of Y‑12 stories highlighting our Construction team.
The Y‑12er spotlight shines on one of our own, Jamie P., Y‑12 subcontract technical representative. It takes all Y‑12 employees to make the mission happen successfully and safely. All views and opinions are the employee’s own and do not necessarily reflect those of CNS.
When Jamie P. stepped into the area she was assigned to at Y‑12, she didn’t have to worry about decorating the walls, as they had been freshly torn down and rebuilt. Her assigned building had been gutted to studs and rebuilt from the floors up as part of a project renovating the facility for new mission work.
Jamie is a subcontract technical representative. STRs serve as the point of contact for subcontractors on‑site.
“My organization helps meet the mission by working with subcontractors to get facilities ready for occupancy. Moving people into a more modern facility helps ensure they can do their tasks efficiently,” she said. “And it improves safety, which is the site’s main priority.”
Jamie chose to work in the construction field because it interested her, especially because of the variety of different job fields under the construction banner. She particularly enjoys learning from other employees and understanding new approaches to the work.
“Construction involves constantly learning and growing as a person,” she said. “I like challenging myself and learning on the job, and at Y‑12, I am learning every day, including new systems and ways of doing work. For example, I learned how much goes into managing the lockout/tagout process, particularly how thorough it is and the steps Construction takes to notify multiple groups and coordinate each group’s response for the process.”
Jamie said what surprised her when she started at Y‑12 was how many construction projects are currently underway across the site. Work at Y‑12 and across the nation to modernize Nuclear Security Enterprise sites echoes the pace of work during the Manhattan Project era as construction teams work projects that will reduce risk, improve safety, and clear the way for future progress.
“Construction is directly supporting the mission by rehabbing old systems as well as building new [systems and facilities],” she said. “This is a fast‑paced environment.”
How has working for CNS changed or reinforced your thoughts on our mission (nuclear deterrence, managing the stockpile, etc.)?
Working for CNS has shown me our mission is more critical now than ever. It’s important that we meet our goals.
What is your favorite aspect about your work environment?
My favorite aspect about my work environment is the people I get to work with every day. They are great to work with and great teachers. Since I was hired on in September last year, I have been learning from my team about how the STR role works and how to run a project from start to finish.
What work advice would you offer someone who is new to Y‑12?
I would find a good mentor in your field and ask them a lot of questions. Asking questions helps in everything I do because I want to better understand what I am doing and why I am doing it that way.
What’s your favorite outside‑of‑work activity and why?
Going to the lake with my friends is my favorite activity outside of work. It’s relaxing.
How has teamwork allowed you to grow as an employee?
Teamwork has allowed me to grow by asking questions about the work and getting to know my coworkers. In Construction, you are always on a team, so teamwork is one of the biggest aspects in my field.
Eric H. began his Y‑12 career as a chemical operator in 2001, fresh out of community college.
The Y‑12er spotlight shines on one of our own, Eric H., deputy director of Enriched Uranium Operations. It takes all Y‑12 employees to make the mission happen successfully and safely. All views and opinions are the employee’s own and do not necessarily reflect those of CNS.
In 23 years at Y‑12, Eric H. has seen and done a lot.
“It’s been a great experience,” he said. “I’ve met a lot of people, and I’ve had the opportunity to be part of different processes and projects. It has been a pleasure to be here.”
He came to Y‑12 as a chemical operator in 2001 and followed that with various roles of increasing responsibility across the Operations organization. Today, he is deputy director of Enriched Uranium Operations. In that role, he assists and fills in for the EUO Director and manages approximately 260 production employees who process enriched uranium into a safe and compliant form for long-term storage, for disposition, or to meet various deliverables such as casting parts for weapons programs or supplying fuel to the nuclear navy, commercial and research reactors, and other customers.
“When I first got here as a chemical operator, I came from construction and agriculture,” Eric remembered. “I came in, got dressed out, and started learning the procedures. It was a challenge to adjust to the rigor and procedural compliance of the nuclear processes being done here.”
Fast forward a couples of decades: “I never would’ve imagined myself in this position. I never planned on being a leader of an organization.”
He came to Y‑12 not long after graduating with an associate’s degree in chemistry from Pellissippi State Technical Community College. He later earned a bachelor’s degree in Organizational Management from Tusculum College, while working at Y‑12.
His first impression of Y‑12 was a case of a dream clashing with reality.
“My vision of Y‑12 was that it was going to be this big high‑tech, spotless nuclear facility,” he said. “But in actuality, parts of the plant were old and dilapidated, two‑thirds of the equipment was not running, and there were many roof and process leaks throughout the work areas. I was not expecting that.”
Although an aging infrastructure can sometimes be a stumbling block, overcoming it is a source of pride for those working to achieve the mission in a challenging environment.
“We get it done, even with the old facilities,” Eric said. “We’re proud of that. There is pride in what we do here, pride in protecting the nation. I’m proud to work here because of the deterrent we are supporting. It’s helping to keep peace.”
How has working at CNS changed or reinforced your thoughts on our mission (nuclear deterrence, managing the stockpile, etc.)?
“Being here has definitely helped me hold a healthy respect for the nuclear industry and why we do this at Y‑12. Perceptions of what we do can keep adversaries from doing something wrong. There’s turbulence and instability across the world. There are countries who may consider launching a nuclear weapon, but then they look at the United States and our capabilities and think twice about it.”
Are you doing what you envisioned as a young adult?
“I envisioned my career to be more hands‑on, more technically oriented. I saw myself working in a lab or in a big chemical facility. Never saw myself assisting in the management of a team of 260 people who are doing the work I thought I might be doing. I’m surprised at where I started and where I am now.”
What’s your top bucket list item and why?
“I would like to visit all of the national parks throughout the U.S. I’ve been to several, like Yosemite and Sequoyah National Park out west. The United States is such a beautiful country. Going to the national parks is a great way to see it.”
We can often become overwhelmed at a work situation. Why is it important to remove yourself from a stressful situation? What advice do you offer to relax and decompress?
“It is extremely important to step away from a stressful situation to help make good decisions. We have to take stress breaks and decompress. For me, decompressing is doing something physical like mowing the yard or riding a bike through the woods. Once you clear your mind, you have a renewed perception and can come up with fresh and productive ideas.”
Matthew S. reflects on being in the same Protective Force as his Mamaw 80 years later.
When Matthew S. walked into a conference room to give a challenge coin to Director of Protective Force Operations and Training Sean K., he did not expect to see a photo of his grandmother on the wall. But there she was in black and white. The lady he affectionately called Mamaw passed away in 2000, but her time as a guard at Y‑12 still lives on through pictures — and through her grandson.
After retiring from his 20‑year career as a police officer and completing a degree in criminal justice at Bethel University, Matthew joined Y‑12’s Protective Force in 2020. Shortly after Sean K. was hired, Matthew remembers walking into the conference room with him and saying, “There’s my Mamaw,” while pointing out his grandmother in a photo featuring the Y‑12 Guard Department from 1945, which was displayed in the room.
Sean K., who was surprised an employee recognized someone from the Manhattan Project‑era photo, asked how Matthew knew, to which he responded he had seen the picture before in his grandmother’s picture book and could pick her out: front row, third from the left.
“I brought in pictures to show Sean featuring Mamaw and another woman — my great aunt Gladys, who also worked at Y‑12. Gladys was not a guard but worked on the site.”
Y‑12’s history is filled with fathers and sons, mothers and daughters, and a workforce that often spans generations among East Tennessee families. But the decades‑long link between Matthew and his grandmother stands out.
Mamaw’s actual name was Helen B. She joined the Auxiliary Military Police at Y‑12 — then known as Clinton Engineer Works — in September 1944. She first joined as a private and then received the rank of guard in January 1946.
“Mamaw did not tell me much about her time at Y‑12; she only mentioned working here a few times during my childhood,” Matthew said.
However, he knows that she was 21 when she was hired and that Y‑12 was the only place she ever worked. He also has memorabilia from her time working at the site, including her certificates of enrollment and photos of her in her uniform.
Helen is one of just nine women who are in the group picture from 1945. In commemoration of her service to the country, Helen received a certificate highlighting the importance of her work for the production of the atomic bomb and the successful conclusion of World War II.
The end of the war brought hope not only for the country and the world but also for Helen, who was waiting for her fiancé, Shelby C., to return from overseas.
When Matthew’s papaw [one of the troops that stormed the Normandy beaches] arrived home from World War II, Helen left work at Y‑12 to marry him and become Helen C. They went on to have four children, the eldest being Matthew’s mother.
“She was a very kind and loving woman,” Matthew said. “A good mother, grandmother, and a good provider. She went to church regularly. She basically raised me and my sister until we went to school.”
Matthew feels the connection to his grandmother is an important one. He did not anticipate ending up at Y‑12 in his career, but he said he is proud to be in the same place she was.
“I know she would be proud of where I am today,” Matthew said. “I wish she was alive to see me working here like she did.”
“What a legacy to be part of the same Protective Force your grandmother served in during the Manhattan Project. It shows that Y‑12 truly is a family environment that has fostered generations of dedication to our region and national security as a whole,” King said.
Matthew added, “Being in the same Protective Force 80 years later is somewhat overwhelming. In 1945, she probably never thought that in 2025, her grandson would be walking the same steps, going in some of the same places that she did. Although some of our job duties may differ now, the mission is still the same, and Y‑12 is still here.
“I’m proud to be here in the same division that she was, and I wouldn’t be alive and here today at Y‑12 had it not been for her.”
When asked what his favorite thing about being a Y‑12er was, he shared, “I feel appreciated here,” which is likely why the legacy of working at Y‑12 often spans generations.
As it turns out, the legacy Helen unknowingly left behind could continue through the next generation, as one of Matthew’s children graduates college in May and already wants to come to work at Y‑12 like his father and great‑grandmother before him.
Among her personal memorabilia is the certificate highlighting the importance of Helen’s work for the production of the atomic bomb and the successful conclusion of World War II.
Construction Trainer Megan S. shares her thoughts on teamwork as part of a series of Y‑12 stories highlighting our Construction team. Photo by Matthew Hawkins.
The Y‑12er spotlight shines on one of our own, Megan S., Y‑12 Construction Trainer. It takes all Y‑12 employees to make the mission happen successfully and safely. All views and opinions are the employee’s own and do not necessarily reflect those of CNS.
Megan S. enjoyed school so much that she wanted to find a way to bring teaching to her day job. While her path landed her as a laborer at Y‑12, Megan imagined how she would share her knowledge and inspire others the way her instructors inspired her.
“The teachers that I had encouraged me to be my best, and I always wanted to give the same,” she said.
That dream became a reality for her when she became a Construction trainer at Y‑12, providing training that the Construction team needs for field work.
“Now I train people with the knowledge that I have and have the opportunity to teach and encourage people to be their best the same way I was taught,” she said.
Megan teaches qualification requirements on Mondays and manages dress‑outs (a practice run of what employees would encounter in a radiological area) on Tuesdays through Thursdays. She also schedules classes, inputs key data, completes documentation checklists, and more to ensure employees receive the training and credits needed to perform daily tasks. Additionally, she manages the computer lab and runs reports for craft and subcontractors. Her favorite part of the job, though, is interacting with the on‑site team.
“I love talking to people, meeting new people, and just getting to know someone’s background and how they got here,” she said.
What stands out to you about Y‑12?
This place is like a little town; there’s so much opportunity at this place — a lot of opportunities to grow and better yourself.
What has surprised you during your time at Y‑12?
One thing that has surprised me at Y‑12 is there is never a day that goes by that you don’t learn something new. You truly learn new things every single day!
What is one thing your coworkers would be surprised to know about you?
The one thing my coworkers would be surprised to know is my family owns Wartburg Speedway. We have owned it for 7 – 8 years now, but racing has always been in my family, about 26 years. My father has raced for as long as I’ve lived, street stock and late model. My dad and I would tear motors apart, wash the race cars, and then he would have me WD‑40 the whole car to make it “shiny.”
Who in your life has inspired you the most and why?
The person who has inspired me the most is my mother. She taught me to be a hard worker and to never depend on anyone. She has always told me if I put my mind to something, to go full force. She had lung cancer when I was a freshman in high school and has been in remission ever since. She’s taught me how to be strong and always told me to never give up on a dream. I always put my all into whatever I am doing because my mom told me if I wanted anything, I’d have to work for it. I hope when it’s my time to be a mother, I’ll be just as great!”
Give an example of how teamwork has helped your role.
Teamwork is an important aspect of Y‑12. If the team doesn’t work together, nothing is going to get done. In my role, teamwork is understanding and listening to what other people have to say, and everyone comes together into a group and figures out the problem.
FIU graduate students Julian Guerra (L) and Brad Alvarez manipulate a haptic glove
On February 17, a Florida International University (FIU) graduate student, Brad Alvarez, placed a device called a haptic glove onto his hand and worked the glove’s fingers, remotely manipulating a robotic hand from a short distance away.
This small demonstration, conducted at the Oak Ridge Enhanced Technology and Training Center (ORETTC), drew a round of applause and big smiles from the observers surrounding Alvarez.
Among them was ORETTC Director Ashley Stowe because he saw the potential this glove could bring Y‑12.
“We use haptic gloves as a training tool in a virtual reality environment,” Stowe said. “They allow workers to do hazardous work training without actually being in a hazardous environment.”
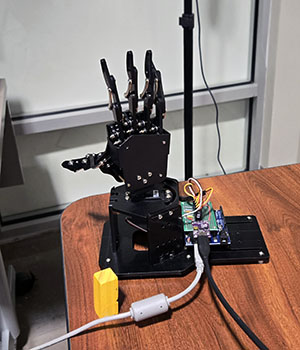
Robotic hand connected remotely to haptic glove. (Photo by Gene Patterson.)
This advancement, Stowe explained, takes hazardous work safety a step further, allowing trained workers to be removed from the hazard while controlling robots in the hazard area to accomplish a task.
“Potentially, this could have a huge impact on how we do work at Y‑12,” Stowe said.
The technology is being developed in partnership with Florida International University. Dr. Shekhar Bhansali heads the program, assisted by Research Scientist Dr. Vivek Kamat.
“We’ve worked with Y‑12 for the past 4 ½ years, and it’s been a great benefit for our students and for Y‑12,” Bhansali said. “It allows us to advance new technologies while training our students in real‑world settings and helps us place students on a career path.”
Those career paths can take the students in many directions. Working with both software and hardware is a big reason FIU students enjoy their time in Oak Ridge.
“We want students involved in this program who are serious about the work,” Kamat added. “These students start from scratch to work a problem, develop a design, and create something new and innovative.”
One of those “serious” students is Miami Native Julian Guerra. He arrived at ORETTC in September 2024 as a co‑op student funded through the Minority Serving Institution Partnership Program (MSIPP). Cooperative education programs, similar to internships, allow students to alternate between academic studies and real‑world practical experiences.
“The partnership with FIU is a shining example of how the MSIPP program can produce top‑tier talents that are uniquely qualified to impact the Y‑12 mission,” Y‑12 Workforce Program Advisor Sanchez Harley said.
ORETTC and FIU partners: (from left) ORETTC Director Ashley Stowe, ORETTC’s Austin Arnwine, FIU Student Brad Alvarez, FIU Instructor Dr. Shekhar Bhansali, CNS Workforce Program Advisor Sanchez Harley, FIU Student Julian Guerra, FIU Researcher Dr. Vivek Kamat, and ORETTC’s Mary Lin. (Photo by Gene Patterson.)
Stowe agrees. “Universities, like FIU, are a vital part of our forward‑looking instructional technology research,” he said. “We, government labs, have a tendency to fall into a standard way of thinking based on our strict regulatory environment. Professors and students bring creativity to our landscape and a different way of thinking.”
Stowe said Guerra has integrated quickly and easily with the ORETTC team and described his work ethic and attitude as “fantastic.”
Guerra says his experience in Oak Ridge has been “more than expected.”
“When I arrived at ORETTC, I would say my knowledge was mostly theoretical, based on coursework and research. My hands‑on experience was limited,” Guerra said.
In just a few short months, that has changed.
“ORETTC has given me a better understanding of what it’s like to work in a rapidly developing industry,” Guerra said. He added the experience was beneficial for him in several ways, including growing skills through hands‑on experiences, collaborating with skilled professionals and subject matter experts, and, most importantly, contributing meaningfully to projects.
“I get to work in a lot of different areas. There’s so much to do. It’s like playing with toys, except in this case, we’re creating really cool stuff,” Guerra added.
Stowe said a benefit from students like Guerra coming and working at Y‑12 is their ability to see problems from a different perspective, allowing industry professionals to be led to new areas — like the haptic glove interface with a robot, which Stowe believes is just the beginning of technology that’s to come.
“These are very bright students who are up on the latest technologies,” Stowe said. “We want to tap into that knowledge base and help them help us. It’s a win‑win.”