Extending reality
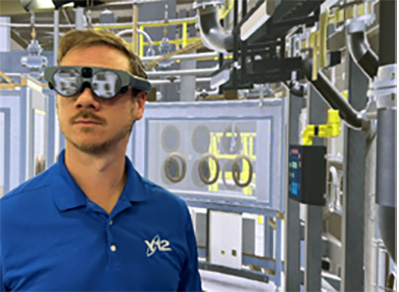
The Y‑12 National Security Complex places trainees in fully immersive virtual environments with next‑generation technologies.
It was a crazy idea, inviting the world’s best Gran Turismo gamers to get in the driver’s seat of a 600-hp Nissan GT3 to become professional race car drivers. So crazy that it actually worked. It worked because Sony’s Gran Turismo acted as extended reality (XR), a simulator that honed in the gamers’ driving skills at high speeds.
Born to be a premier facility for training in emergency response, nuclear security, and advanced technologies, the Y‑12 National Security Complex’s Oak Ridge Enhanced Technology and Training Center (ORETTC) uses XR in a similar way to train in scenarios that would be dangerous if done in the real world.
The Emergency Response Training Facility on the ORETTC campus not only focuses on training first responders but also on training Y‑12 operators on low‑occurrence, high‑consequence scenarios by using next‑generation technology, such as augmented reality, virtual reality, mixed reality (MR), and haptic feedback gloves. Funded by the Plant Directed Research, Development, and Demonstration (PDRD) program, these XR training simulations are best‑in‑class and act to fully immerse the trainee into a virtual environment through the use of these next‑gen technologies coupled with high‑fidelity digital twins developed in simulation engines such as Unreal Engine and Unity. These simulations are identical to real‑world physical spaces, persons, processes, systems, and products.
“Advances in XR have already changed the way we work, live, and play, and it’s just getting started,” PDRD Program Manager Mark Richey said. “XR literally takes ‘hands‑on’ to a whole new level. We are excited to be part of such research.”
Digital Twins and Internet of Things
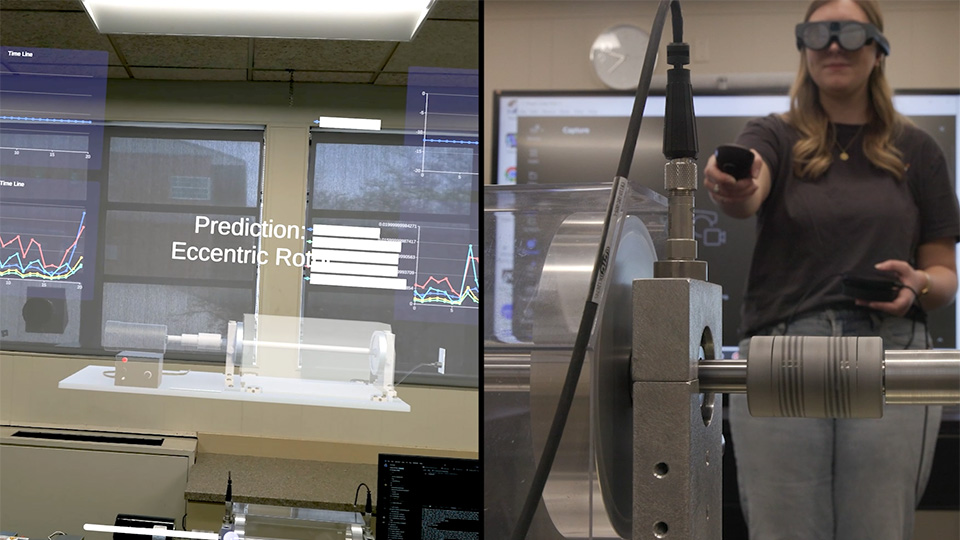
A University of Tennessee student operates a motor remotely through an XR headset and hand controllers while collecting data about the motor’s functionality.
ORETTC has unlocked Internet of Things capabilities in highly secured environments by developing a complex system engineering ecosystem that enables virtual XR headsets to access and retrieve data from real devices in a separate location. “We are able to remotely operate a motor,” said Mary Lin, interim director of ORETTC. “We can be here at ORETTC and turn on that motor at our partner facility at the University of Tennessee, Knoxville, to gain pertinent data. It’s pretty exciting.”
“The purpose of the Digital Twins and Internet of Things project is to send virtual commands to a device and also be able to read live data from a physical device as it runs,” explained Austin Arnwine, instructional technology lead. “This information loop will enable us to predict maintenance needs on machinery before it requires maintenance and even send the responsible operator the most up to date training needed to fix the machine before it needs it.”
“Y‑12 is developing digital twins at various scales,” said Scott Couture, senior director, Production Research, Development, and Integration, adding that the investment also helps create tools for other projects. “Digital twins are tools. They are a simulation at some level to help you solve a problem, such as improving the capacity and reliability of a machine.”
ORETTC applies new technology and science in a very short time frame with the goal of obtaining end products so when XR technology or machine learning advances to the next level, the technology can be integrated quickly.
“It’s so exciting! We’re not just doing the technology and science but also the application of that technology in a very short time frame,” added Tom Berg, joint adjunct assistant professor at the University of Tennessee, Knoxville. “We want to take this XR technology and machine learning to produce end products and reduce it in practice. It has so many applications outside of Y‑12!”
Collaborative XR
In the workforce today, XR is being used in many ways to collaborate with people in person and at a distance. A great example is a surgeon on the east coast who can consult with a peer/surgeon on the west coast using a secured network. This XR technology enables the ability to operate or work with a patient and meet their needs in real time while another professional is on the line.
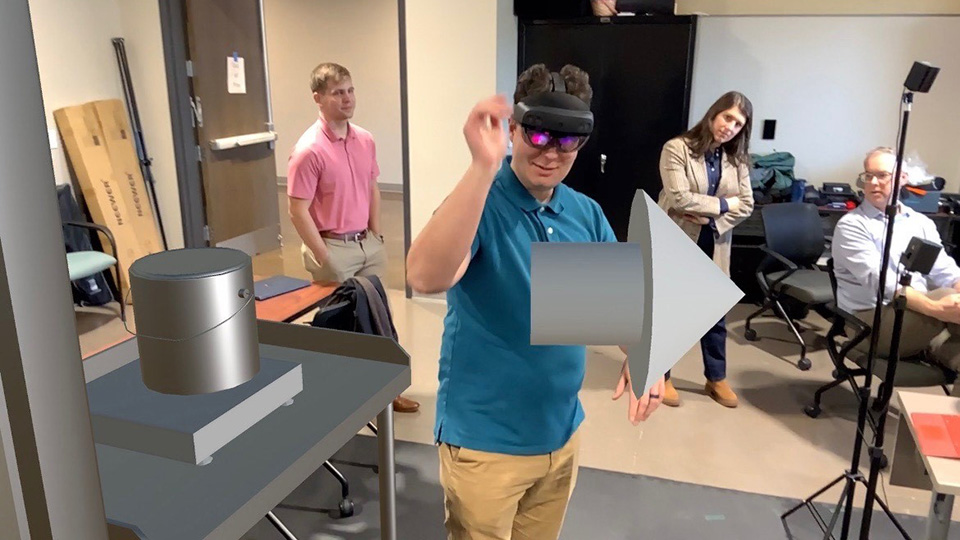
An operator is showing virtual additive manufacturing capability in a collaborative XR environment.
“The Collaborative XR project is about humanizing digital data,” explained Erik Nykwest, Y‑12 Development multi‑physics scientist. “You can set your digital asset on the table side by side with your real‑world product and compare them. You can pick up data with your hands and literally stick your head inside of it, exploring it in ways you would have never dreamed of with a two‑dimensional computer monitor. XR is an enabler that allows people to interact with digital objects as if they were real, and the collaborative aspect enhances communication and clarity when discussing complex topics.”
ORETTC has enabled this capability for additive manufacturing through funding from PDRD. Using a collaborative XR platform, ORETTC can now use headsets, tablets, and computers to convert traditional computer‑aided design (CAD) and computed tomography (CT) scans into 3‑D visuals for manufacturing and production team collaboration. This capability enables the ability to troubleshoot operations efficiently and to make design decisions without any interruption on the shop floor. These collaborations and consultations can be done in person and at a distance, as ORETTC can ship headsets to other Nuclear Security Enterprise sites for end users to collaborate as if they are in the same room.
“This technology is an evolution of how people work together moving forward,” said Arnwine. “Collaborative XR will facilitate real‑time improvements in processes and products without the need of building complex physical test models or travel for in‑person meetings.”
“For a designer or technician to be able to see what’s happening with a product or system without being in the same room is a game changer,” said Derick Weis, assistant PDRD program manager. “These platforms will facilitate real‑time improvements in processes and products.”
Haptic Feedback in Mixed Reality Glovebox Training
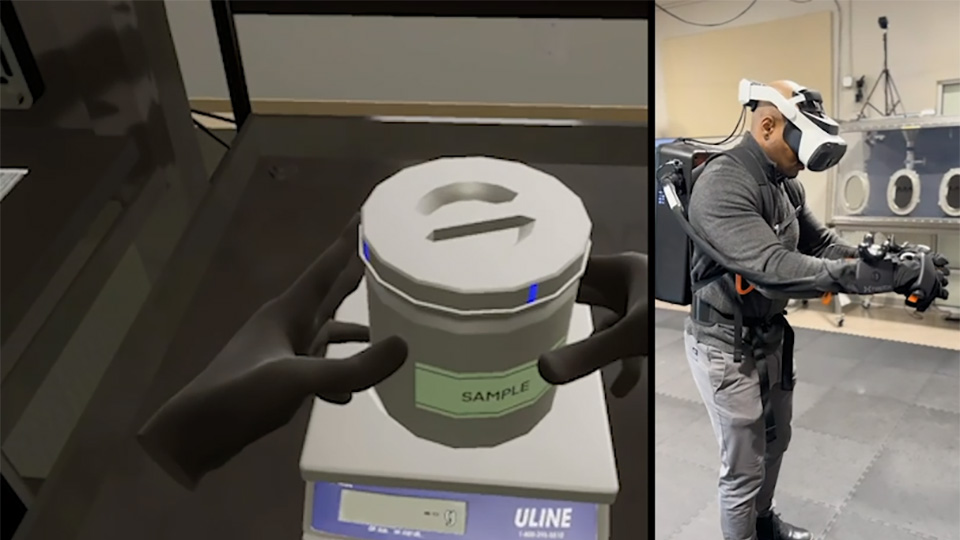
Using haptic feedback, a Y‑12 trainee works virtually to gain an understanding of the parameters of working within a glovebox.
The sense of touch and its subsequent feedback is a natural sensation often missing in XR experiences. Due to the nature of the U.S. Department of Energy’s manufacturing, dealing with sensitive materials through gloveboxes is highly touch‑driven. These glovebox jobs can be very high consequence, depending on the materials handled. ORETTC has spent the past 3 years perfecting a simulation that enables the sensations of force and texture feedback in the hands of end users in an XR training experience.
“Through the multi‑sensory engagement (touch, pressure, texture, and resistance) offered by the haptic feedback glove, chemical operator trainees feel immersed in real‑life situations while practicing conduct of operations, following procedures, and learning how to handle unlikely, but high‑stress, critical situations,” said Kim Nickell, Production Activities Training manager. “Trainees have the opportunity to practice high‑risk scenarios without real‑world consequences. Trainers are able to work with participants until the desired outcome is achieved, all while providing immediate feedback on decisions and actions that are made.”
This training experience uses haptic feedback gloves, an MR headset that the U.S. Department of Defense commonly uses for flight simulators, and a physical glovebox to simulate a material sorting exercise for new glovebox operators. This training is now being considered for placement in the Y‑12 training pipeline, as it has been tested and approved by the Y‑12 Training group and their leadership. This work was also published in “Frontiers in Virtual Reality” in March 2025 (Frontiers | VR haptics for glovebox operations training).
“With haptics in our training arsenal, trainees are getting an instructional experience that feels real,” said Weis. “It’s getting the trainees up to speed faster than traditional training methods.”
“It has been a privilege for our Production Activities Training team to work with ORETTC in the development of the Haptic Feedback Glovebox Training,” stated Nickell. “We are excited to see the future of training at Y‑12 as we adopt cutting‑edge technologies.”
Advancing XR Research and Development
“PDRD is honored to support ORETTC’s commitment to researching and developing new XR technologies and how those technologies could directly advance the manufacturing industry and NNSA’s core mission,” concluded Richey. “Through exploration of cutting‑edge solutions in immersive digital twins, haptic feedback systems, collaborative XR, and next‑generation XR environments, Y‑12’s ORETTC is driving innovation and addressing real operational needs.”
These advancements enhance workforce readiness, improve safety, increase precision, and streamline complex processes. Through strategic partnerships and forward‑thinking research, Y‑12 lays the groundwork for a more agile, capable, and future‑ready manufacturing ecosystem. Our efforts ensure that we remain at the forefront of technological progress, shaping the industry and setting new standards for excellence.