Y-12 Blog
Y-12 Engineer Katie Romba, posing with one of her paintings
Engineering is defined as the “creative application of scientific principles to design or develop structures, machines, apparatus, or manufacturing processes.”
The term engineering is derived from the Latin ingenium, meaning “cleverness” and ingeniare, meaning to “contrive or devise.”
At Y-12, engineers help guide our mission work, often using clever, if not ingenious, methods. They troubleshoot problems and create solutions that make our work more efficient and better.
Engineers are also sometimes given certain stereotypes: math-whiz, fact-focused men.
However, engineers can be so much more. Engineers like Katie Romba are proof of that.
A 2019 Clemson graduate, she was hired at Y-12 into the Career One program. She’s worked rotations in Design Engineering, Specialty Mechanical (now Production Equipment Engineering), and is currently working on Development on the Technology Transition Project team, which is helping Y-12’s technology modernization efforts.
Engineering is her day job, but her passion is art.
“I got really serious about my art in my teens,” Romba said. In high school she entered the Congressional Art Competition, winning not once, but two years in a row. Her artwork was showcased in the U.S. Capitol building.
“Most of my work specializes in photo-realistic pieces and my go-to medias are acrylic painting, watercolor, marker, and colored pencil.
“My art captures what life is like around me,” she said.
Judging from a large part of her portfolio, what is around her is food. Growing up, she was plagued by childhood allergies.
She found herself allergic to almost every major food allergen (milk, wheat, eggs, peanuts) and so she couldn’t eat many of the things everyone else could.
“Instead, I would draw these foods, study their texture and color, and imagine what their flavors would be like through art.”
Since moving to the Oak Ridge area, Romba has become involved with the Dogwood Arts Festival. She’s been an exhibitor at the Dogwood Arts House and Garden Show Makers Market. She also joined the Tennessee Artist Association and participated in their fine arts programs.
In 2021, Romba opened the doors to her own studio, making art an official business and fulfilling a lifelong dream.
Despite that, she’s still very grounded and serious about her work at Y-12 inside the blue line.
“I enjoy the challenge that is offered in my work every day. There is always an opportunity to design a creative solution to a project’s needs, and I enjoy searching out opportunities to create a more efficient and better functioning work environment for our projects,” said Romba.
Romba also enjoys the challenge of growing her art. “My goal is for more of the community to experience my work by showing more pieces in galleries, both in the Knoxville area and around the country, and connect with others in the way we see the world around us,” she said.
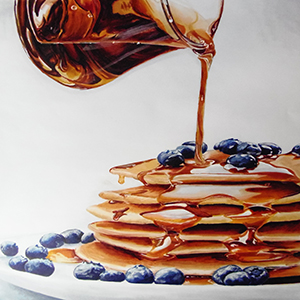
One of two new cranes that will assist in the rolling and forming processes for depleted uranium.
Some workers at Y-12 now have a safer work environment thanks to the installation of two cranes. Y-12 Project Management and Construction completed the project in just three months, six months ahead of schedule.
The new cranes support depleted uranium forming and rolling. A salt bath crane, which travels north to south, is used to remove billets from a salt bath to the rolling mill, where they are flattened into pancake shapes. A load table crane, which moves from east to west, transfers billets to and from the salt bath crane. Both have remote controls, which make them safer to operate, and are equipped with digital scales to weigh hoisted material.
“The old cranes were unreliable and way past their useful life expectancy,” said Rodney Howard of Production Projects.
To add the new cranes, the team learned from the installation of an older argon-pit crane.
“They’re all similar cranes—bridge-type cranes,” said Construction Manager Billy Hurst. “With the first one we installed years ago, we ran into some issues with the mechanical portions of the crane itself. Because we used some of those lessons learned from that, we did not have any installation change requests. We didn’t have anything that got in the way. We were able to use those lessons learned on the first one toward these two we installed. That mitigated a lot of things that could’ve gone wrong.”
The lessons learned help facilitate “rigging for the demolition of the old crane and installation of the new one,” Hurst continued. “We installed lifting lugs above the cranes to the existing building structure, enabling us to accomplish the demolition and installation without having to build extensive cribbing or other rigging configurations. It also helped in relation to the crane stops and some bolt installation. We had to reconfigure with new bolt fasteners that didn’t protrude and obstruct the crane movement and travel.”
Most projects encounter more than a few bumps on the road to completion. It was a relatively easy path for this one.
“It was near perfect in regards to design effort, procurement of the cranes, and all that comes into play,” Hurst said. “They fit up perfectly when we put them in place on the existing crane rails. Sometimes you have to adjust for different measurements, but these were spot on.”
Hurst believes this experience can be used as a blueprint for future endeavors.
“Granted, these are not really huge projects, but it’s just rare that you ever have a project without hiccups,” he said. “I guess we did the right stuff, and we documented it. We are able to pull out that documentation and use it in the planning process for any other installation.”
Properly disposing of the old cranes and railings also addressed a safety concern with lead-based paint, which would flake off.
“People don’t realize the challenge of the waste disposition,” Hurst said. “You have to drain the oil. It has to be treated differently. Then some components have contamination, and others have to be segregated out and go a different path. Craft and laborers had to dispose of it and get it loaded, positioned right in containers so they’re balanced, and ready to be shipped.”
Hurst credits the success of the project to a team effort.
“It’s craft, the project manager, the construction manager, the superintendent, field engineers,” he said. “It was a good team. Plus, we did it safely without any injuries or incidents.”
Remote controls allow the machines to be operated from safe locations.
Anyone who has stepped foot onto Y-12 National Security Complex is aware of the importance placed on safety. Trainings, signs, procedures, and more are all put into place to help employees and visitors return home in the same, if not better, condition than they arrived. For one employee, remembering a random safety fact from a training long ago and implementing a small but impactful change is attributed to helping save her life during a recent wreck.
Quality Assurance Specialist Susan Donnelly was driving a rental SUV on I-81 in Virginia to a trail race she’d been waiting two years to attend. She was in the left lane when she came up over a hill to see traffic at a standstill. She stopped quickly and easily behind the next car in her lane but worried that any vehicle coming behind her would not stop successfully.
Donnelly kept watch in her rear-view mirror and immediately saw the movement of a vehicle dodging its stopped lane and changing into hers. All she had time to do was push the brake pedal and brace herself.
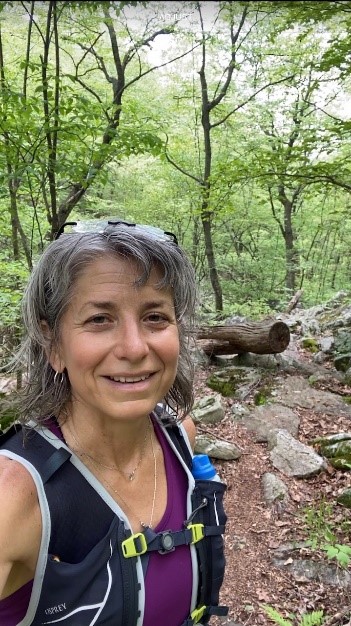
Quality Assurance Specialist Susan Donnelly
“I heard the violence of the crash — sound of glass shattering and metal smashing, the vehicle bouncing up and hitting the vehicle in front of me, and everything in my SUV flying everywhere — and then silence,” she said.
Donnelly was taken by ambulance to the hospital, given x-rays and a CT scan, and was told she had suffered bruised ribs and airbag burns on one arm and her knees. The emergency room doctor explained that he had expected to see more damage.
Just thirty minutes before the crash, Donnelly randomly remembered a safety meeting at work from years ago that explained how close a driver should sit to the steering wheel.
“I remembered it was around twelve inches, so I estimated it, decided I needed more room, and scooted the seat back,” she said. “I checked that I could reach the gas and brake — all fine — and forgot about it, until after the wreck.”
The simple act of shifting herself back from the steering wheel might be what saved her life, or reduced the possibility of serious injury.
“A paramedic I talked to after the wreck said remembering that tip from a long-ago safety meeting was probably why I walked out of the ER,” Donnelly said.
“While on-site, employees are provided regular safety information with the goal to develop a safety culture where employees look out for hazards and complete work in a safe manner,” explained Julie Cramer, Y-12 Safety and Industrial Hygiene Senior Manager. “We also want employees to bring that information and mindset home. Employees will see many of the same safety risks off site and if we can keep people safe at work and influence them to be safer at home, that’s a win-win.”
“Take it from me, something small you hear in a safety meeting could prevent debilitating injury and save your life,” said Donnelly.
One of the New Employee Orientation classes during 2022 at Y-12’s New Hope Center.
Starting any new job is overwhelming, but starting work at a nuclear weapons production site is even more so. Human Resources and Communications led an effort to improve the onboarding experience for new hires at Pantex and Y‑12, with substantial engagement from other organizations. The goal was to create an onboarding experience that empowers employees with a clear understanding of our mission and enables them to contribute to our mission more quickly.
The enhanced orientation program acquaints new employees with goal‑setting, provides intensive employee training with presentations about both sites, and connects each new hire to an organizational ambassador from his or her business area. By the end of orientation, new employees have a deeper understanding of their individual roles in achieving the mission. They also have a clearer organizational picture, familiarity with the Pantex and Y‑12 strategic plans, and continued support through the connection and relationship built with their organizational ambassador.
As an organizational ambassador, Leslie Mathews of Y‑12 Production Operations provides one‑on‑one support to new employees during their first 90 days of employment (and often longer). “I hired in almost 15 years ago,” she said. “I did not get all of this information on day one. It takes lots of time to understand the magnitude of what we do, but with the onboarding structure, new hires have the opportunity to learn so much at the very beginning.”
“The engagement of senior leaders and organizational ambassadors in onboarding has been a game-changer,” said Senior Director of Communications Jason Bohne. “New employees are not only learning how they connect with the mission but are also gaining perspective on our priorities and beginning to build a network of people who can help them be successful in the short term and throughout their careers. Welcoming them and giving them the tools to succeed helps make us all successful.”
Making sure new employees are introduced to how they fit in our national security mission falls to Recruitment and Placement Specialists Zuleyma Carruba-Rogel and Jay Aspray.
“We’re always asking ourselves, ‘Is this the best that we can be?’ That constant reflection and adjustment lets us know we’re on the path to success,” Carruba-Rogel said. “When we see and experience the community that new hires are creating; when they respond to content and tell us they feel welcome; or when they talk about what a great experience onboarding was for them — that’s when we get to reap the fruit of those labors.”
Pantex Deputy Site Manager Kenny Steward said, “In our sites’ histories, we have rarely had to compete with a broad range of employers to attract talent to Pantex and Y‑12. Orientation is one of the opportunities we have to show new employees that they made the right choice and have joined a team they can be proud of for the rest of their careers. It’s our new employees’ introduction to life and culture in a high‑hazard, nuclear production environment, allowing us to set the stage for tying each employee to our critical nuclear deterrent mission and ensuring they know the dramatic value they add to the important work done at our sites.”
At the Global Security Analysis and Training Learning Lab, the use of different virtual or augmented headsets allow people to communicate with others across great distances for common objectives.
The Oak Ridge Enhanced Technology and Training Center (ORETTC) is under construction on the west end of the Oak Ridge Turnpike. It will be a state-of-the-art training complex that serves as the nation’s preeminent training facility for radiation response, nuclear processing, and emerging technologies. However, some of the ORETTC technology has been getting a trial run across town.
While ORETTC is being built, the training for radiological emergency responders has continued at Y-12. Relatively new to the mix is the Global Security Analysis and Training (GSAT) Learning Lab. The facility sits a short distance from the Y-12 site and its success is due in part to the challenges posed by COVID-19.
“We went from having all these face-to-face engagements to needing to do virtual engagements,” said Mary Lin, senior manager of Knowledge Acquisition and Performance Studies (KAPS).
She said technology became the solution.
Within the walls of the lab are instructional designers with expertise in video and technology. There is an attorney on staff for nuclear safeguards and policy instruction.
“Our augmented reality program came to life out of the COVID-19 pandemic. Our distance learning and virtual-learning-use green screen technology. All that came out of the pandemic,” said Lin.
Green screens allow participants to be placed into virtual locations that simulate real-life scenarios.
“One of the things that we do with green screens,” said Lin, “is play videos, similar to a news production, allowing a person to point out things in the video for better comprehension. We also use iPads that let them be John Madden, who was famous for diagramming football plays on monitors. It allows [instructors] to kind of circle the event in a video and say ‘look at what’s happening.’ So it creates that immersive learning experience.”
Participants are offered a full menu of training resources. “We do everything from international engagements to domestic training, where we offer everything from alarm response training to international nuclear material accountancy and control courses,” Lin said.
Toby Williams, who heads GSAT, said the courses being developed at the learning lab will benefit all its programs and create a better learning environment.
“Augmented reality training allows us to engage with participants in an immersive manner in both in-person training and distance training,” Williams said. “It makes the training and concepts more interactive, which means the participants are more likely to remember what we taught,” he added.
Being off-site also has the benefit of lowering the risk level GSAT potentially presents to the site.
“Security is a huge deal at the site and understandably so. Moving to ORETTC will reduce the level of risk we present to the site, allowing us to challenge new processes, ideas, and concepts. Specifically, within our international engagements, we will be more adaptable.” said Williams.
Ashley Stowe is the new director of ORETTC.
“The GSAT group provides nuclear and radiological response training to our customers. The learning lab is a place where we develop the technologies and the course materials to deliver to our customers,” said Stowe. “In the gaming universe, they use this type of technology on a regular basis.
The use of different virtual or augmented headsets allow people to communicate with others across great distances for common objectives. It’s the same for us, but these are just toys until we provide the educational component, which the KAPS team provides.”
Stowe said working with their customers and subject matter experts, they are creating real-life simulations with gaming attributes. Add the educational component, and participants receive an enhanced training experience.
Stowe, Williams, and Lin all said the center will promote and challenge critical thinking in high-consequence operations or emergency response events, and will create a more adaptable and efficient training curriculum.
ORETTC is located on an 81-acre campus in Roane County within the City of Oak Ridge. It will consist of two facilities, the Simulated Nuclear and Radiological Activities Facility and the Emergency Response Training Facility, and will serve as a graduate-level academy for first responders, nuclear security professionals, and nuclear nonproliferation experts.
Stowe said they intend to host their first ORETTC training class with outside participants in early December.
Activities such as radiological material moves can be simulated in the Global Security Analysis and Training Learning Lab.