Y-12 Blog
NNSA Principal Deputy Administrator Frank Rose (right) shakes hands with Y‑12 employee and local hero Brody Roberts during a recent site visit. “Meeting Brody was a highlight of my trip to Y‑12. He is a stand‑up example of excellence in character,” said Rose.
Y‑12 employees go above and beyond at work each day to deliver on the site’s national security mission. But the commitment to excellence doesn’t stop at the end of the day. During recent winter weather, one employee literally jumped into action to save a stranger in need.
Even with an impending forecast of snow, it was a typical evening for Brody Roberts, Y‑12 project waste engineer and Roane County resident. After a full day of running errands and eating dinner with his family, Roberts decided to hit the gym before the roads became dangerous. But shortly after leaving the restaurant, his evening turned from typical to terrifying.
“I had been driving for five minutes before I approached a truck in the road,” Roberts recounted. “As I slowed down I looked at the lake and saw a car out there. My first thought was, ‘How I could help?’”
He immediately pulled over and jumped out. “There was a person on the phone with 911 who mentioned someone was still in the car,” Roberts explained.
Roberts sprang into action. Removing his outer layer of clothing, he jumped in the frigid water. As he reached the vehicle, which had just completely submerged, he opened the door and saw a woman was still buckled. Roberts and the woman unlatched the belt, and he helped her swim to the surface.
“As soon as we made it to the surface, I was instantly relieved,” Roberts said. “I was even more relieved when she said she was the only one in the vehicle.”
After swimming to dry land, a group of bystanders wrapped Roberts and the woman in coats.
“It was the coldest I have ever been,” said Roberts.
The woman was taken to a nearby hospital with non‑life‑threatening injuries, and Roberts decided he could skip the gym.
When asked why he decided to jump into the near‑freezing lake, risking his own life, Roberts replied “I was only doing what I hope others would do for me and my family.”
Y‑12 employee Michael Laws stands in front of the house from which he pulled two children during a recent fire.
It has been proven time and again that Y‑12 employees are not only an asset to CNS, but also to the communities in which they live. Recently one employee showed great bravery by saving two children during a life‑threatening situation.
As Y‑12 quality specialist J. Michael Laws was ushering his family into the car for a quick shopping trip, he received a call from his neighbor.
“She told me that she thought her house was on fire, that she and her husband were at the movies and their two daughters, ages 14 and 7, were home alone,” Laws explained.
Thinking the girls had burned something in the oven or that an appliance had possibly caught fire, Laws and his wife grabbed a fire extinguisher and headed across the cul‑de‑sac in their Hardin Valley neighborhood.
But as soon as they crossed the road, it became clear that the situation was much more dire.
“I could see the girls in an upstairs window and could hear them crying out that they couldn’t breathe,” said Laws. “My wife began calling 911 as I tried the door, but it was locked, so I kicked out a window and began climbing in — but it was too hot and smoky.”
Laws quickly realized he would need to bypass the home’s ground floor due to the fire.
“I ran back to my house while screaming for help,” he said. “Fortunately, there were people in earshot who ran over. I grabbed my ladder, ran back across the street and got it set up just as one sister climbed out of the window and bravely jumped down to two people.”
Laws quickly climbed the ladder, and pulled the other child to safety as black smoke started billowing from the house.
“I knew right then if we had not been home or missed that call, those girls would not have made it,” said Laws.
The children were quickly taken to Laws’ home where they waited for the fire department, ambulance, and their parents.
“They were, of course, in a panic, but they were so courageous and did all the right things,” he said. “My wife got them water and began consoling them while my kids started gathering toys, clothes, food, and whatever they thought our neighbors may need.”
For Laws, this experience highlighted the importance of having a disaster plan for those in your home.
“My main takeaway is that you have to have a plan,” he said. “We have discussed one, but have never drilled or practiced in any way. We will be doing that very soon.”
He also noted the importance of community and watching out for one another. “Community is important,” explained Laws. “Even my children felt the innate call to help our neighbors in need and immediately answered. I believe our neighbors would do the same for us, and I am proud to be a part of this community.”
A special touch: Holding to the masons’ tradition, a 1943 coin, the year Building 9731 was built, was placed into the pavement.
It’s a nondescript yellow brick building just down the hill from the Jack Case Center at the Y 12 National Security Complex. The building could be easily ignored as an inconsequential structure, but looks can be deceiving. Recently, the look improved a bit.
Building 9731, known as the Pilot Plant, is Y-12’s oldest structure. Constructed in 1943, it housed the first of what became more than 1,100 calutrons across the site. Calutrons were the electromagnetic machines that separated the uranium isotope U 235 from U 238, enriching the uranium to bomb grade and providing material for Little Boy, the first of two atomic bombs that helped end World War II.
The building’s historic significance has placed it and Building 9204 03 (Beta 3) in the footprint of the Manhattan Project National Historical Park. Established in 2015, the park’s three units extend from Oak Ridge to Los Alamos, New Mexico to Hanford, Washington. All were vital pieces in the mission to build an atomic weapon.
Susie Smiddy is Building 9731’s manager and has been working with Y-12 infrastructure to enhance its look and utilization.
“I’ve been working to make Building 9731 a premier facility that reflects the important values, character, and powerful history of the building since 2018,” Smiddy said.
One of the obstacles to enhance the building’s character was the front entrance. The concrete was broken and uneven, and there was gravel where an old storage shed used to sit.
“I contacted Darrel Watkins, the site’s planner for masons, and we worked on a design that would maintain the historic nature of the entry area. We sat together over several months sketching out ideas and patterns,” she said.
They also consulted masons Jeff Webb and Noah Sexton.
“Jeff and Noah spend a lot of time — plant wide — making our sidewalks and entryways safe. They suggested replacing the entire entry area. During the planning process with Susie, we recognized an opportunity to truly make it better, and reintroduce a style that encompasses the building’s rich history,” Watkins said.
The solution they chose was to pour, stamp, and color concrete at the entrance. The finished product stays true to the historic nature of the building, but it is also a showcase of the artistry and craftsmanship of the masons involved in the project.
But it wasn’t just the masons, as others were also integral to the project. Carpenters Corey Brown and Paul Oakes built lean tos for the masons when rain threatened the work, and they built the frames for each section of the pour, in addition to framing the two ground wells.
This took a team effort from the masons and carpenters, to the laborers who added river rock to the entry, to the heavy equipment operators and pipefitters,” said Smiddy. The process took a lot of planning and communicating. “Darrel and I talked directly with Jeff and Noah, not only as we planned the project, but up to the day they started performing the work, making adjustments along the way.”
The final special touch, holding to the masons’ tradition, was to place a 1943 coin, the year Building 9731 was built, into the pavement.
“So often with much of the aging infrastructure at Y-12, it’s simply fix what needs to be fixed and move on,” said Watkins. “This project presented an opportunity to actually step out and produce something that instills pride in our site and in the workmanship of our craftspeople.”
“My hope, as we continue to preserve this facility, to expand the tour route, and repurpose it for the training mission to ensure long term sustainment, is that we create something that everyone can be proud of,” said Smiddy.
Zuleyma Carruba-Rogel engages a class of new employees at Pantex.
Take a few minutes and learn about Consolidated Nuclear Security’s Jay Aspray (Recruitment and Placement specialist at Y-12) and Zuleyma Carruba Rogel (Recruitment and Placement specialist at Pantex) and their roles with New Employee Orientation. All views and opinions are the employees’ and do not necessarily reflect those of CNS.
Pantexans and Y-12ers know this isn’t your typical nine to five job. Making sure new employees are introduced to how they fit within our national security mission falls to Recruitment and Placement Specialists Zuleyma Carruba Rogel and Jay Aspray.
“I make it clear on the first day that there isn’t a single person in that room who is there by chance or by luck,” said Carruba Rogel. “The interview process is very detailed because we’re not just looking at skill — we’re looking at fit. Each person in that room is there because one, they’re the cream of the crop, and two, they proved to us through all these processes that they share our mission before walking in that door.”
The Department of Energy mandates specialized training for all employees hired at nuclear sites. At Pantex and Y-12, General Employee Training covers site specific safety and security. But by itself, GET doesn’t provide a complete picture of what new employees will encounter on the job. That’s where onboarding specialists Aspray and Carruba Rogel step in, setting a positive tone for orientation, guiding discussions, and reinforcing understanding of mission success and company culture.
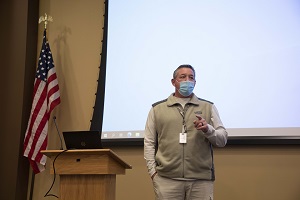
Jay Aspray guides in-class discussion with new employees at Y-12.
“We’re always asking ourselves, ‘is this the best that we can be,’ and that constant reflection and adjustment lets us know we’re on the path to success. When we’re in that room and can see and experience the community new hires are creating; when they are responding to content and telling us they feel welcome; or when they reach out and talk about what a great experience it was for them — that’s when we get to reap the fruit of those labors,” said Carruba Rogel.
An enhanced orientation program, developed in Texas and later updated and expanded to Tennessee, acquaints new employees with goal-setting under the Mission Success Model, breaks up intensive training with enterprise level presentations and interactive skill shares, and assigns new employees 90 day peer advisers called “ambassadors.” By the end of orientation, new employees have done more than check off mandatory training — they also have a deeper understanding of their individual roles in achieving the mission, a clearer organizational picture, familiarity with the Pantex and Y-12 strategic plan, and a peer ambassador relationship for continued support.
“The new onboarding process positively impacts mission success by providing new employees with the right tools and useful information for a smoother transition in joining the team,” said Aspray. “New Employee Orientation is centered around the Mission Success Model, and the course agenda provides a strategic focus on the enterprise’s capabilities, allowing new employees to become more adept at mission delivery.”
What work advice would you offer someone who is new to Pantex or Y-12?
Aspray:The Army is known for mottos and acronyms, so early on in my career I decided to create my own motto — something I could stand for daily. I decided on Triple H, for “Happy, Humble, and Hungry.” Every day I would ask myself three questions: “Are you happy,” “Are you humble,” and “Are you hungry”? If I answered no to any of the three questions, I would analyze the “why” and do my best to fix the situation immediately. So my advice would be to create your own motto, something you can stand by daily — something meaningful and close to you that will help you be successful, professionally and personally.
Carruba Rogel: You’re not going to have too many other opportunities where your hiring managers recognize that you have a steep learning curve. It’s okay to be the learner as opposed to the expert or the one passing down information. One of the things I insist on for new employees is to be aware of their learning style and to be mindful that people teach in the learning style they’re dominant in. For example, a visual learner might like PowerPoints and written notes, but their manager might be an oral learner. Because you’re in this steep learning curve, make sure you negotiate those spaces so you understand what you need to do and how to do it. Try repeating back, “So this is how you mentioned I should do such and such; is this what you want?” Be mindful and negotiate that space to take what you need to adapt and start making the impact you want to make.
What top strength do you bring to your organization and why?
Aspray: I believe one of my top strengths is commitment. I enjoy what I do and the mission is meaningful, which makes my commitment to this organization easy. I spent 29 years in the Army, and I had a sense of pride with purposeful work for the nation. I was uncertain I was going to find this kind of work once I retired from the Army, but the transition was smooth, and my commitment is still stronger than ever.
Carruba Rogel: I’m very aware of cultural environments. I’ve done a lot of work like this where I’ve been in front of people. When I get a new group, I come in and get a sense of what the feeling in the room is and how I can get them to start peeling off these layers so they’re taking as much as they can from this experience. My favorite aspect of onboarding is working — in a very deliberate and calculated way — to help create a sense of family, belonging, and value.
What do you love about recruiting?
Aspray: When you look at the impact of what we do, it not only affects the new hire but also impacts each family in such a positive way that you have to be happy about what you do.
Carruba Rogel: When you hear the excitement and you know these offers — they’re changing people’s lives, not just for themselves, but for their families. And the best part is seeing our new hires at orientation.
Wayne Carlton helps guide Y-12 to become a more recycling friendly workplace. Those efforts have earned him a Lifetime Achievement Award from the Department of Energy.
Take a few minutes and learn about Wayne Carlton, an environmental engineer at Y-12. All views and opinions are the employee’s own and do not necessarily reflect those of Consolidated Nuclear Security.
At home, Wayne Carlton handles the trash, with a little “help” from his wife.
“I have to separate everything,” he said. “She tends to put it all in one container.”
At work, Carlton deals with the waste of thousands of employees as an environmental engineer at Y-12, where he is a major contributor to the plant’s successful recycling and sustainability efforts. Because of his decades of work in those areas, he was given the Lifetime Achievement Award during the Department of Energy’s 2021 Sustainability Awards, which recognized outstanding sustainability contributions of individuals and teams at DOE facilities across the country. In addition to Carlton’s honor, Y-12’s Recycling Program was honored with the Outstanding Sustainability Program Award for its long term recycling efforts. In FY 2020, the program recycled more than 3.8 million pounds of materials, which resulted in $1.1 million in cost avoidance.
“I was humbly surprised,” he said about receiving the award. “As you work over the years, you do things because they need to be done and because you enjoy doing it. You don’t think about awards.”
Carlton’s career, which began at Westinghouse Hanford Company in Richland, Washington, spans 40 years. He came to Y-12 in 1989 as part of the Clean Air Program, in which he assisted operations personnel prepare air permit applications for submission to the Tennessee Department of Health and Environment.
“I have many jobs,” Carlton joked. Currently with the Y-12 Site Oversight Agreement Program, he monitors the development of information to fulfill the Oak Ridge Reservation Environmental Surveillance Oversight Agreement among DOE, the National Nuclear Security Administration, and the State of Tennessee. ESO assures Tennessee citizens that their health, safety, and environment are protected by DOE. In that role, he liaisons with government officials and external agencies. Also, Carlton is an auditor and inspector at treatment, storage, disposal, and recycling facilities, where he assesses their ability to meet requirements for handling, transporting, processing, and disposing DOE waste and material.
“I conduct audits at places where we send waste,” he explained. “It’s vendor verification. We have to make sure they live up to the contract and are compliant. A place can look really good on paper, but sometimes when you go out there, it’s like no, no, no. We don’t want things from Y-12 floating down the river.”
Those “things” could include a wide range of recyclable materials, from aluminum beverage cans and tires to cooking grease and toner cartridges. Also on the list are wood pallets, which are taken away monthly and ground into mulch.
Carlton serves as a system administrator of the site’s Environment, Safety, and Health directorate as well. In that role, he is responsible for the upkeep, configuration, reliable operation, and management of information technology desktop assets. Carlton advises and assists the Sustainability and Stewardship Program on technological improvements and the disposition of electronics. Also, in this position, he initiated and coordinated projects that integrated modern technology into various directorate operations. In addition, Carlton was integral in the replacement of the site-wide shredder and participated in the installation of BigBelly® solar powered, rubbish compacting bins, which provide a visible electronic warning when they are full.
At Y-12 for more than three decades, Carlton has seen the plant and society make major strides in recycling and sustainability.
“There’s been real progress the last 20 years,” he said. “Recycling has become more convenient now. If you make it more convenient, people will do it. It’s a mindset. If it feels like a chore, you won’t do it.”
Are you doing what you envisioned as a young adult? If so describe how you got here.
I wanted to be an engineer, so I did that. But I also envisioned myself making a real contribution. Didn’t want to be just a consumer.
What is your favorite aspect about your work environment? How does that aspect make you know the mission is being met?
Taking on a project and seeing it come to fruition. You will have pitfalls along the way, but there are always solutions for everything.
What work advice would you offer someone who is new to Pantex or Y-12?
Don’t be afraid to fail. Work outside your comfort zone. Learn something new. Take on a challenge. Never just go through the motions. Keep on growing. Also, don’t think things are going to come to you automatically.
What is your favorite outside of work activity and why?
I love landscaping, doing electrical work, any kind of do it yourself projects. Really enjoy doing things with my hands. The only thing is that my wife says I don’t do the projects fast enough.
What one thing would your coworkers be surprised to know about you?
When I retire, I want to teach people about computers, be a real advocate for them. I want to help bridge the gap between technology challenged people and computers, help them get rid of the fear they have of them.