Y-12 Blog
Rack framed and wrapped for shipment at supplier’s facility
Racks, or “multi-commodity pipe rack modules,” are one of the many components that go into building the Uranium Processing Facility. Achieving 100% rack delivery required tremendous effort and planning, but the team completed the feat ahead of schedule.
The magnitude of the task was considerable, including processing and reviewing thousands of documents and coordinating consistent communication with the supplier. The team’s efforts paid off with a smooth acquisition and delivery process.
Overall, the team procured 295 racks at a total cost of approximately $60 million. Hitting 100% rack delivery opens up many work fronts for construction, allowing them to stay on schedule and move to the next goal.
The first request for proposals (RFP) for the racks was issued in August 2018 and awarded in February 2019. The last delivery was in summer 2021. The team is evaluating lessons learned throughout the three-year journey that can be used in the future.
“One-hundred percent rack delivery means we are one step closer to completing UPF. Finishing this enormous endeavor ahead of schedule displays how hard our team has worked to achieve our goals; in fact one of our critical 2021 UPF goals. Thank you to everyone who dedicated their time and efforts to design, procure, and receive these essential elements in building our nation’s UPF,” said Dena Volovar, UPF Project Director.
Brandon Grogan (right) from Oak Ridge National Laboratory is the most recent participant in the Mid-Career Professional Exchange project sponsored by National Nuclear Security Administration’s Office of Nonproliferation and Arms Control. The project seeks to provide production experience to researchers. Jeff Preston (left) of Y-12 Development served as Grogan’s mentor.
Oak Ridge National Laboratory (ORNL) and Y-12 National Security Complex (Y-12) both trace their history to the Manhattan Project, and both play important roles when it comes to international nuclear safeguards. International nuclear safeguards are a set of technical measures applied by the International Atomic Energy Agency on nuclear material and activities, through which the IAEA seeks to independently verify that nuclear facilities are not misused and nuclear material is not diverted from peaceful uses.
The Mid-Career Professional Exchange project, sponsored by the National Nuclear Security Administration’s (NNSA’s) Office of Nonproliferation and Arms Control, seeks to educate researchers through a production experience. This project provides ORNL staff members a fresh perspective by giving them working-facility experience and mentorship with a facility expert from Y-12. The ORNL employee leaves Y-12 with real-life applications for their current research and development ventures, and better prepared to serve the international safeguards community, while Y-12 is able to tap the employee’s expertise in areas such as computer modeling and nuclear detection.
Since 2018, Y-12 has hosted several exchanges. Brandon Grogan from ORNL's Material Security and Stewardship group is the most recent staff member to participate in this program.
According to Y-12’s principal investigator, Jason McCall, this exchange was very successful. “Brandon was able to complete an accelerated exchange, despite the challenges of COVID-19. He spent time in the Highly Enriched Uranium Materials Facility and our other production and fabrication facilities, and he was able to learn a lot of new skills that are directly applicable to international nuclear safeguards.”
Research vs. production
With a B.S. in Physics from West Point and an M.S. and Ph.D. in nuclear engineering from the University of Tennessee, Knoxville, Grogan has the academic bona fides. He’s been at ORNL since 2006, starting as a graduate research assistant. He is now a staff researcher, and his interests include nuclear forensics, international safeguards, non-destructive measurements, and inverse methods.
The career exchange allows Grogan to add some production experience to his impressive academic résumé before he goes to his next assignment as a technical advisor for the Nuclear Materials Information Program in Washington, D.C.
Jeff Preston of Y-12 Development served as Grogan’s mentor. “Brandon had visited a few other sites, but he had not worked in the production areas, so this exchange allowed him to see how a production facility operates. While he is going to an M&O (management and operating) position immediately afterwards, I believe the experience here will help shape how he approaches his role regarding production sites.”
Give a little, gain a little
As a “computer modeling guy,” Grogan brought some unique skills to Y-12. “I can model things that are too expensive or too dangerous to measure,” he said. The results of his computer simulations provided unique insights into Y-12 materials for various radiation detection applications.
While working in Development, he focused on a system for measuring oxygen content in various materials. The previous system was assembled in the 1990s, and replacement parts are no longer available. Grogan’s goal was to develop models for new system designs. With these models, Preston’s team will be able to select and purchase components for the new system, confident that it will achieve the same measurement fidelity as the old one.
The bottom line
“The career exchange is a good program that provides cohesiveness and team building between NNSA and Office of Science laboratories,” said Preston. “Office of Science personnel rarely obtain an in-depth view of an NNSA production facility given need-to-know and other limitations. The program enables a cross-pollination between labs and production sites that can better align strategic goals.”
As the Y-12 program lead, McCall wants these mid-career exchanges to be formative. “I hope Brandon’s experience at Y-12 contributes to his success throughout his safeguards career,” he said.
“It’s definitely been worthwhile,” said Grogan. “We (researchers) do all this theoretical stuff, and we sometimes forget what a production environment looks like.”
ORNL’s program lead, Jessica White-Horton, further touts the exchange: “When the participants return to ORNL, they are reinvigorated and communicate about how much they have learned! Some things simply cannot be taught in a classroom.”
All community colleges are expected to educate and train students to prepare them for a future career, but Roane State Community College goes a step further. At its Harriman campus, Roane State established the Raider Pantry, a facility that provides supplies for students dealing with the issue of food insecurity.
“It’s difficult to be your best in class if you’re worrying about feeding your family or yourself,” said Karen Brunner, RSCC’s vice president of institutional effectiveness and a co founder of the food pantry project. “Since September 2019 when we opened the pantry, hundreds of students, their children, and other family members have been served.”
With the pandemic creating a national emergency, the need for food increased as many families struggled with their finances. Through the Neighbor to Neighbor Fund, a $2,500 grant from CNS was matched with a $2,500 grant from East Tennessee Foundation, which provided much needed support for RSCC’s COVID-19 crisis response.
With many students learning from home amid the pandemic, RSCC hosted “Food Pantry On the Go” events that attracted students and their families who might not otherwise have been able to take advantage of the service.
“We had one student who drove in for the event and she had her kids with her,” said Dr. Lisa Steffensen, RSCC’s dean of students and a food pantry organizer. “We helped her pick out some items and made sure the kids got to help pick cereal and a dessert item to take with them. As they were leaving, one of the kids yelled from the back seat, ‘Thank you for helping us.’ It just really hit home how much these meals mean to our students and their families.”
The east side of the Uranium Processing Facility's Main Process Building
The Uranium Processing Facility (UPF) at the Y-12 National Security Complex successfully completed all third-level walls and concrete roof placements for the Main Process Building (MPB) on Wednesday, September 29, marking a major milestone for the UPF Project. This signifies the completion of structural construction for the MPB.
Construction work on the MPB began in 2018, and the interior construction and commissioning will be completed by the end of 2025. The MPB is one of seven UPF subprojects and the largest single building on the project. The 242,000-square-foot structure was built to nuclear construction standards, once completed and fully operational, will house casting, special oxide, and some chemical recovery processes.
The MPB subproject includes the construction and installation of the building as well as site preparation, long-lead procurements, the installation of the Perimeter Instruction Detection Assessment System (PIDAS), and a connector to the Highly Enriched Uranium Materials Facility (HEUMF).
“This milestone marks a major shift for our construction team on the UPF project,” said Dale Christenson, UPF Federal Project Director. “UPF construction team demonstrated the teamwork and tenacity necessary to complete the MPB structure working through the challenges that East Tennessee weather brings, and allows a majority of the work to be performed indoors.”
Construction will continue on the interior of the building as crews install key process modules, gloveboxes, and additional process equipment throughout the next few years. The remaining interior construction also includes additional work for subcontractors on heating and ventilation ductwork, fire protection piping, and interior finishes.
“Completing the structure for the MPB is a major achievement for the project as we continue to build our nation’s UPF,” said Dena Volovar, UPF Project Director. “We are moving the project forward, and we recognize it is vital to get the job done right. We have the right team to deliver UPF, and this achievement shows the great work that is being done each and every day.”
UPF supports the nation’s Uranium Mission Strategy, which ensures the long-term viability, safety, and security of enriched uranium capabilities in the United States. UPF will replace casting, special oxide production, and salvage and accountability capabilities from a World War II-era building with a modern and more efficient facility for conducting highly enriched uranium processing operations at Y-12 National Security Complex.
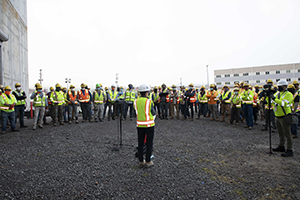
Dena Volovar, UPF Project Director speaks to craft personnel at the Main Process Building Civil Structure Completion Ceremony
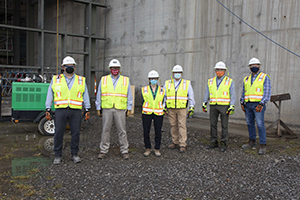
From Left to Right: Mike Robinson, Bechtel UPF Project Manager; Dale Christenson, UPF Federal Project Director; Dena Volovar, UPF Project Director; John Howanitz, President of Bechtel NS&E GBU; Gene Sievers, Y-12 Site Manager; and Jim Sowers, MPB Area Manager
This LiveWise mural brands the renovated fitness centers and makes the centers easily recognizable.
Some rejuvenating reps have the East and West LIFE Centers at Y-12 looking pretty buff.
The 11-year old structures have received makeovers. They now boast fresh paint, power washed and replaced trim, and new eye catching murals. Inside the West site, bathrooms sport new flooring, and ceiling tiles have been replaced.
“We’re excited to present the updated facilities,” said Consolidated Nuclear Security’s Health and Wellness Supervisor Karen Lacey. “They are a real value to employees. This helps set the tone for the importance we place on wellness and the health of our people, the most important resource.”
The centers have two different color schemes. East is cream with gray trim, while West is also cream but with red accents. They provide a backdrop for two of Lacey’s favorite additions, the LiveWise murals.
“Now it’s branded,” she said. “The logo makes them easily recognizable, easily distinguishable. People now know that it is part of the LiveWise Program.”
The renovations have been in the making for some time.
“It’s been 3 years trying to put this together,” Lacey said. “It started coming together in the spring, when we were able to get funding.”
The East and West centers are smaller offshoots of the larger fitness facility at Jack Case Center. They feature cardio and strength equipment, and change houses are next door. Like the JCC location, both are open 24 hours, 7 days a week. The centers have more than 4,000 usages each month.
In addition to the fitness equipment, there are LiveWise classes, such as outdoor boot camp sessions and virtual yoga. New to the roster is functional fitness training, which offers workouts in a small group setting. It focuses on exercises that train muscles to work together and prepares them for daily tasks by simulating common movements done at home, work, or in sports.
“I think this will attract some new people to the center,” Lacey said. “It’s a little less intimidating than taking a class with a lot of people.”
LiveWise also offers discounted (or free) registration to sports events, mobile mammography, and other health education programming.
“We’re as good as any gym in the community,” Lacey said, “and it’s always free. We’ve just saved employees 30 bucks a month.”
Members of the crew that made the upgrades possible gather at the East LIFE Center