Y-12 Blog
Demolition of Building 9720 22 at Y 12
More than ever before, the landscape of Pantex and Y-12 is changing. In FY 2020 alone, 46 infrastructure projects were completed, and an impressive 21 facilities (11 at Pantex and 10 at Y-12) were demolished.
Diane McDaniel, senior director for Excess Facilities Disposition, has challenged the disposition team with a stretch goal to achieve 100 total demolitions within the years of FY 2015 and FY 2021.
“The disposition team is made up of approximately 50 individual contributors representing all organizations at Y-12 and Pantex. These team members, along with an outstanding subcontractor community and the NNSA Production Office, are the key to the program’s success. Because of their dedication and focus, the CNS disposition program is held up as the example for the other NNSA sites across the country,” McDaniel said.
CNS teams worked diligently to meet their FY 2020 goals during the COVID-019 mission critical operations so that they would be ready to hit the ground running to accomplish as much as possible within the safety envelope when they returned to the site.
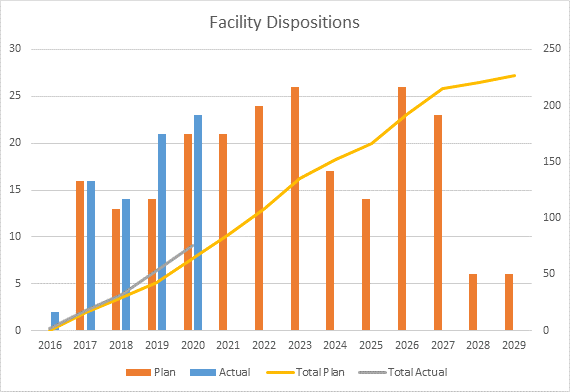
“We have never attempted, much less achieved, that many dispositions and square footage of almost 30,000 square feet this year at Pantex,” said Pantex Excess Facility Disposition Program Manager Jennifer Simms. “We continue to achieve more facilities and square feet every single year. We are really ramping up and changing the landscape of the site one demo at a time.”
“Demolitions are important to reduce the site footprint and eliminate facilities that present significant hazards. We have to remove the old to make way for new mission essential facilities,” said Y-12 Excess Facility Disposition Program Manager Kevin Bradford.
“Because we are reducing the footprint with demos, it gives us the opportunity to work with NNSA to obtain the funding needed for new facilities,” said Laura Fox, Pantex Projects Management. “These new facilities will provide greatly improved working conditions for our personnel, as well as provide greater reliability of facility systems.”
Planning for demolition starts no less than two years before the building is actually torn down. Many times, characterization of hazards within and around the facility, location and condition of utilities, and other factors must be known ahead of even starting the drawings that must be produced and provided to contractors for bid.
“Taking down old facilities is always challenging,” Fox said. “Many times, the drawings from when these facilities were constructed are either not available or are unreliable.”
She said it is truly a team effort between organizations including Projects, Procurement, Engineering, Construction Management, and the contractor who work hand in hand to overcome issues and get these buildings down.
New behind the scenes challenges for FY 2021 demolitions are already being reviewed for another 21 planned demolitions next year and more than 25 in FY 2023.
Heroes don’t always wear capes (but they do wear face coverings). These three Y-12ers jumped into action to help a Kentucky man suffering from dementia. (from left: Chris Griffis, Mark Butcher, and Jack Bolinger)
Most Y-12 employees try to be helpful. Last month, three Y-12ers proved that statement when they were in the right place at the right time.
Chris Griffis, Jack Bolinger, and Mark Butcher were driving near the Horizon Center on Highway 58/95 when they spotted someone in the road.
“He looked to be in distress, and we stopped to see if he needed help,” Griffis said.
The three got out of the car and asked the man if he needed assistance. The man was confused, couldn’t answer any questions, and had a wound on his head.
Bolinger said, “The more we talked to him, the more it was apparent that, at the least, he had a concussion. He couldn’t tell us who he was, where he was headed, or where he came from. He thought he was in Kentucky. He was barely making coherent sentences.”
Bolinger called 911, and the three stayed with the man until the paramedics arrived.
“Everyone is always in a hurry, and I get that, but take time to figure out someone’s situation,” Butcher said. “You should always look to lend a helping hand, especially when you can improve or help someone else’s situation.”
The paramedics took him to the hospital for evaluation. Later that day, Bolinger received a call from one of the paramedics that the man was suffering with dementia and had been missing from Kentucky.
Griffis said, “Sometimes the world we live in seems quite dark; however, there are many more good people in the world than people who would wish to do you harm. You absolutely need to be aware of your surroundings for the safety of you and your loved ones. Conversely, there are people everywhere who could use some assistance in one form or another. You never know how much a seemingly small gesture can mean to someone who needs it.”
“Something that is often missing from people’s actions are doing them from a service perspective, where nothing is in it for them,” Bolinger said. “If you see a need, take action! Never underestimate the impact you can have in someone’s life by a seemingly insignificant action.”
These good guys advise to look for places where you can help. Griffis said, “It’s vital in our country right now to help those who truly need it.”
It pays to be alert, and when you see something — even someone in distress — say something. Thanks to these three Y-12ers, the missing Kentuckian was soon home.
When it’s time to perform factory acceptance testing on a critical technology during a pandemic, what do you do? Since the product still must be delivered, you adapt by monitoring the work remotely.
Pre-pandemic, CNS and NPO staff would have sent several people on multiple trips to observe electrorefining testing. This time, because of COVID restrictions on the number of people allowed in the shop, the project team could only send two representatives.
With limited access and high stakes - electrorefining is key for uranium processing - the project team had to figure out how more of them could view the testing. By purchasing some iPads and communicating via WebEx, the team remaining in Oak Ridge could effectively monitor the testing and communicate with the team members at the vendor’s site. Project manager Steve Cruz said, “We had a learning curve with WebEx, but it was manageable.”
From a conference room in Jack Case Center, the NNSA customer and Production team members were able to monitor the testing that was being conducted across the country in one of Merrick’s facilities. In fact, some team members were able to view the testing from their computers on site or while teleworking.
Cruz thinks viewing factory acceptance testing remotely may be advisable even when travel isn’t restricted. “With remote viewing, staff who only need to see a small portion of the testing can do so without the expense of travel,” he said. The remote viewing also allows parties who are interested to witness the testing, too, which may be helpful to train staff to observe such tests in the future.
Remote testing may have been born of necessity, but the benefits, including reduced travel costs and ease of staff participation, may remain when we reach the “new normal.” Watch this short video (closed captioned version) for more information.
Project manager Steve Cruz participates in factory acceptance testing for electrorefining remotely.
Development’s Trevor Roberts, Direct Material Manufacturing lead, isolates several key samples to be sent to Y-12’s Analytical Chemistry Organization.
The National Nuclear Security Administration’s (NNSA’s) Office of Defense Nuclear Nonproliferation (DNN) works globally to prevent state and non-state actors from developing nuclear weapons or acquiring weapons-usable nuclear or radiological materials, equipment, technology, and expertise. Through the Office of DNN Research and Development (DNN R&D), NNSA advances its nuclear threat reduction mission by developing ways to detect and monitor foreign nuclear fuel cycle and weapons development activities.
This summer Development, the Analytical Chemistry Organization, Program Integration, Mission Engineering, and Environment, Safety, and Health leveraged ongoing Direct Material Manufacturing and completed the second campaign in isolating select lithium samples.
Consolidated Nuclear Security (CNS) Chief Scientist Greg Schaaff said, “When people think of nuclear nonproliferation and forensics, most think of the production and use of uranium and plutonium materials. However, the production of lithium compounds are central to civilian energy and military applications.”
Matthew W. Francis is the Pantex and Y-12 contact with DNN R&D. He said, “Using Y-12’s lithium processing and applications core capabilities, DNN R&D has funded a collaboration between CNS, Lawrence Livermore National Laboratory, and Los Alamos National Laboratory to determine potential signatures capable of differentiating between civilian and weapon applications of lithium compounds.”
“In our initial subsampling campaign in FY19, we had to overcome many challenges along the way,” said Jason McCall, program manager of Global Security and Strategic Partnership Programs. “Challenges included failed coring tools, answering questions on contamination, and coordinating with other projects in regards to schedule and priority. Trevor Roberts was essential in getting us through these challenges, as well as many others. By the time we started ramping up the second subsampling campaign in FY20, our initial challenges were a distant memory. Trevor and the entire Direct Material Manufacturing team were key in making our subsampling campaign a success.”
Following the subsampling efforts (which is when a sample is drawn from a larger sample), several lithium samples were shipped to ACO to run through several measurement methods to identify a variety of trace elements.
“ACO sees many new matrices that push our current analytical capabilities,” Tom Oatts, ACO lab supervisor, said. “Through the use of innovative approaches to existing lab methods, Sarah Slack and other ACO team members can push these capabilities to meet our customers’ needs and requirements.”
Francis said, “While this project is still ongoing, accomplishing these campaigns was essential for the overall success of the project. This effort could not have been executed if it wasn’t for the great collaboration across the various Y-12 organizations.”
Sarah Slack of the Analytical Chemistry Organization separates key trace elements that potentially could be used for differentiating between interdicted lithium samples.
Y-12 Apprenticeship Program 2020 graduates present their diplomas. From left: Jacob Scarborough, electrician; Christopher Drinnon, pipefitter; Brandon Muir, pipefitter; and Dustin Wilson, electrician.
After 13 years as a Y-12 laborer, Christopher Drinnon acted on his father’s advice: “You should get in a trade.” Now a recent pipefitter apprentice graduate, Drinnon graduated on October 6 from the Y-12 Apprenticeship Program alongside three skilled journeymen, one pipefitter and two electricians.
Since 2008, Y-12 has celebrated 97 graduates and eight graduation ceremonies in the program. Before graduation, each apprentice is trained to union specifications for journeymen level classification upon completion of the program. In addition to qualifications, apprentices learn from experiential training opportunities and work three month rotations in different workshops throughout Y-12. Through these experiences, apprentices gain valuable knowledge in their field and on site.
“The Apprenticeship Program has positioned Y-12 for long term mission support, at a time when skilled craft workers are in high demand,” said Will Farmer of Y-12 Infrastructure. “Our program is a great way to transfer knowledge from highly skilled workers to the new workforce and is our guarantee that we will be able to meet our future production goals,” he continued.
A combined partnership between CNS and the Atomic Trades and Labor Council, the Apprenticeship Program is registered with the Department of Labor as well as the Veterans Administration. Y-12’s Joint Apprenticeship and Training Committee is also involved to guarantee the welfare of the program by meeting each month to address various topics on how to grow and assist the program.
Apprentice supervisor and JATC member Zach Yost said, “Our committee exists to ensure that we’re nurturing unsurpassed talent for our program. Today, it’s safe to say that we’ve found that here with our 2020 class.”
The graduates also were recognized for not only their hard work but also the sacrifices that were made by the apprentices and their families.
“The main lesson was not to give up,” said Brandon Muir, Y-12 pipefitter. “The experience was an adjustment; adding 3.5 hour classes, two nights per week on top of a 10 hour day was challenging.
That’s not counting my commute and having a new baby, but the on-the-job training made it worth it.”
In honoring the graduates, Y-12 Site Manager Gene Sievers emphasized the significance the skilled trades have on the mission and the development of the men and women who follow in their footsteps.
“Being skilled in the art is extremely important,” he said. “Your knowledge and capabilities are foundational for Y-12’s enduring mission, our national security, and the future generation of skilled trades.”
With milestones met, Y-12’s four new journeymen will progress to a new chapter making their impact to on site operations and continuing the legacy and strength of our workforce.
“This is a great accomplishment for you, CNS, and our union. This is something that can never be taken from you and will provide you a path to a career that you can be proud of,” said ATLC President Mike Thompson. “I know and appreciate the sacrifices you have made to achieve this graduation. But it doesn’t end here. You will continue to learn and become more proficient in your skills. The responsibility you face couldn’t be more important. You are the ones who will take our place and carry on the proud tradition of being some of the most skilled tradesmen in the world.”