Y-12 Blog
A key principle at Y‑12 is continuous improvement — one of 11 principles that reflect the site’s commitment to being a learning organization. Twice a year, the Performance Improvement group asks Y‑12 organizations to submit projects to be included in its “Continuous Improvement Celebration.” There, each team shares its successes, and employees vote for the Best Y‑12 Initiative and Best Value Stream Element Teams Initiative.
This year’s recent celebration included 14 projects — 10 Y‑12 initiatives and 4 VSET initiatives.
The Tooling Project Team pictured standing in front of a machine on the shop floor.
The Best Y‑12 Initiative: The Tooling Project Team
The Tooling Project Team, comprised of Jeremy P., Adam F., Brian F., and Bill T., worked proactively to identify and mitigate problems with the tooling production system, which supports the Master Production Schedule. The Master Production Schedule is based on demand from Y‑12’s external customers and is used to align shop floor schedules across all production facilities on‑site, allowing major production deliverables to be met on time.
The group noticed that there were challenges concerning data integrity, priority management and integration, and communication between stakeholders. These challenges had been preventing Y‑12 from reliably aligning the shop floor schedule with the master schedule. As a result, the site faced a risk of production delays due to tooling not being delivered on time.
The team acknowledged these challenges and standardized schedule priority integration for tooling orders. To further monitor and improve their capacity for tooling movement, they created a visual dashboard to communicate scope and schedule data to all stakeholders and created a system of metrics and key performance indicators for the tooling production system.
The results of their work brought 15% fewer hours spent in tooling manufacturing labor despite an 82% increase in volume of tooling produced compared to the prior fiscal year. Other benefits included:
- A $44.7M return on investment as a result of increased manufacturing throughput
- A reduction of risk to program schedules, specifically risk regarding tooling readiness
- A compilation of current and historical data and metrics to be used for tracking, analytics, forecasting, and estimates
The team’s new tooling scheduling has enabled General Manufacturing to be integrated into the master schedule of site deliverables for the first time.
“This project provided a lesson learned moving forward,” Adam, a recent graduate from the Y‑12 — University of Tennessee Master’s Cohort program for Systems Engineering, said. “We can now prioritize the consistent flow of information and shared understanding of priority, enabling the shop floor to focus on fulfillment of orders and reduce disruptions in product flow.”
Adam also presented the project as his capstone project in the UT program.
“It was a great experience to apply the material from my coursework to the project,” Adam said. “The human factor — focused approach to systems engineering is something I will continue to use in my career from now on. I am proud to contribute to the mission, and I feel obliged to do whatever I can within my influence to improve our ability as a site to do so.”
Team member Jeremy said, “I view continuous improvement as paramount to our mission because each year, we are asked to do more and more as a site. If we do not make changes, we will be unable to keep up with demand in the coming years.”
The Best VSET Initiative Winner: Beta 2 Operators Reorganization Team
Marcus M. and his team “saw a need and took initiative” and was named the Best VSET Initiative across the site.
The team identified a problem with the organization of their supply room. Due to the room often being unorganized, it was difficult for employees to find consumables in a timely manner and know when to place reorders.
“I think it’s great that our team was a winner,” Marcus said. “A lot of hours went into making this storage room what it is today, and I couldn’t have done it without the help of many operators. At one point, there were over 20 people who helped with this project.”
1. Sort 2. Set in order 3. Shine 4. Standardize 5. Sustain |
Marcus and the team used 5S, a methodology that results in a workplace that is well organized, free of unneeded items, safe, and conducive to high quality outputs. The reorganization team sorted and disposed of unneeded items, set in order every item that is needed in a way that supports operations, and implemented a Kanban system to sustain the progress made. A Kanban system is an inventory control system that uses visual cues, like cards, to manage production and indicate when more supplies need to be ordered.
“Our team learned the value of Y‑12’s Clean Sweep program and the importance of visual management,” Marcus said. “These two tools allowed us to dispose of unneeded items and learn a new system that leads to operators actually taking pride in this room now.”
This team’s efforts saved 73 hours annually spent on looking for consumables.
“You know you started something great when people want to become involved, and that’s great,” Marcus said. “Operators have taken initiative to help improve and finish up certain jobs to ensure that the room stays organized. Continuous improvement allows workers on the frontline to have a say in how their work atmosphere is maintained. It inspires growth, and growth is good.”
The unorganized supply room before the team of operators took the initiative to make it more efficient.
During her Y‑12 tenure, Heather Harrison has held a variety of roles, all that prepared her for her current role as Nuclear Engineering director. Photo by Matthew Hawkins.
The Y‑12er Spotlight shines on one of our own. It takes all Y‑12 employees to make the mission happen successfully and safely. All views and opinions are the employee’s own and do not necessarily reflect those of CNS.
When Heather H. graduated with a degree in industrial engineering from the University of Tennessee in 2002, she had plans to take a job at a meat packaging company.
She changed her plans when she heard about the work being done at Y‑12.
“I didn’t know a lot about Y‑12 until a good friend of mine shared about it,” she said. “The mission intrigued me. I learned more and was even more interested after that.”
Heather joined the Y‑12 team in a time of tumult; the site was heavily recruiting as many in the workforce were approaching retirement, while also following heightened security guidelines after the 9/11 attacks the year before. At the time, 50$ of Y‑12’s workforce was eligible to retire, and some clearances were taking 2 years to process — Heather’s included.
Since then, she has worked in a variety of positions across the site, whether as a technical advisor, a project lead, or now as Nuclear Engineering director. She currently oversees Nuclear Criticality Safety, Packaging Engineering, and Fire Protection Engineering.
“Over the years, I’ve had so many great managers and mentors that shared information and gave me opportunities to grow,” she said. “Now I’m here at 23 years of company service and it’s my turn to pay it forward.”
One way that she is paying it forward is through a focus on encouraging and building confidence within her employees. With the recent reorganization of Nuclear Engineering, Heather has taken the opportunity to bring her team through continuous improvement training.
“I want people to learn the framework, learn how to make decisions, and know their authority to make those decisions,” she said. “I encourage setting healthy boundaries and let people make decisions within their ability.”
When making decisions, Heather has a simple goal:
“I focus on continuous improvement,” she said. “Decide on a solution and gather data. It’s alright if your decision was the wrong one; the key is to keep improving. Sometimes we get bogged down with worries over whether we’re making the wrong decision, when we need to make the decision to improve regardless.”
What is your favorite aspect about your work environment?
The people. I have the opportunity to work with very talented individuals and enjoy working with this team to overcome obstacles and support the mission.
What CNS principle drives you to be successful?
Operational Excellence. As an industrial engineer, I’m a firm believer in continuous improvement, data‑driven decision making, and customer focus. I also believe alignment with the business strategy and employee empowerment are keys to being successful.
What work advice would you offer someone who is new to Y‑12?
Be willing to accept a challenge and step out of your comfort zone. I’ve had some really great opportunities over my years at Y‑12 because someone saw potential in me, even if I didn’t see it yet.
What is something you are looking forward to doing in your role?
I am a new director for Nuclear Engineering, and we are completing a reorganizing strategy. We are establishing several new positions like direct charge supervisors in Nuclear Criticality Safety. I look forward to watching these individuals establish themselves and grow as leaders. It’s exciting for me to watch these individuals enter these new roles.
What advice would you offer a newer employee about the importance of solving problems and asking questions?
It’s important to understand what you know, what you do not know, and what the requirements are surrounding the problem you need to address. This helps you to better understand your gaps and when you may need additional help in addressing your problem. There are a lot of requirements that cover our scopes of work, and it’s important to ensure that all the right questions have been asked. Failure to ask an important question can lead to a major issue in one of our nuclear facilities.
Installation Dog was a Y‑12 uranium storage facility from May 1948 to May 1949 that was disguised as a silo (shown above) and a barn. The area later became known as Katy’s Kitchen and now is part of the Oak Ridge National Laboratory.
In the article below, writer Amy A. shares details about working on a 2004 Y‑12 cookbook.
As a Y‑12 employee, I’ve experienced a number of blessings in my 30‑plus years, but one of the most memorable happened in 2004 while working on Katy’s Kitchen: Y‑12 Secret Recipes. This cookbook was funded by Y‑12’s managing and operating contractor with proceeds going to Y‑12’s United Way Campaign.
The title for the cookbook came from a former Y‑12 storage facility used from May 1948 to May 1949. First known by the code name “Installation Dog,” and designated as Building 9214, the original purpose of the facility, which was located on the Oak Ridge National Laboratory (ORNL) site, was to house enriched uranium after World War II.
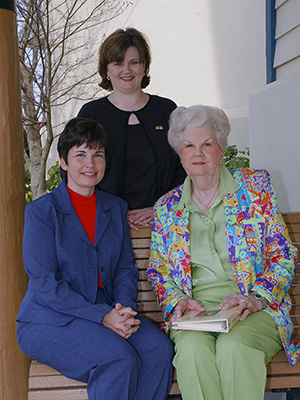
Y‑12ers Elaine W. (left) and Amy A. (center) met Kathryn Odom Howard in April 2005 to share the Katy’s Kitchen: Y‑12 Secret Recipes cookbook.
History buffs Mick Wiest and Ray Smith, both Y‑12 employees at the time, had shared with me how the secure building came to be built by Luther Agee. According to the historians, Agee never knew how or why he was chosen to design the structure, but he was told Installation Dog would be a secure building and would store bomb‑grade uranium. When built, Installation Dog was disguised as a barn and silo to camouflage it in East Tennessee’s rural farming landscape. Before completion of Installation Dog, Building 9213, an uncamouflaged facility located on the Y‑12 site, was used for storing the uranium.
In my research, I learned how Installation Dog was renamed Katy’s Kitchen after Kathryn Odom Howard in the late 1950s. During Howard’s time at X‑10 (what ORNL was referred to then), the three Oak Ridge sites (K‑25, X‑10, and Y‑12) were under one contractor. Her organization, Analytical Chemistry, was located there, and Howard often had lunch there. The group decided to nickname the facility “Katy’s Kitchen,” and the name stuck.
Working on the cookbook gave me a behind‑the‑scenes look at Y‑12’s history, offered the opportunity to work with a great crew of people, and allowed me to meet the namesake of Katy’s Kitchen.
After the cookbook was published in 2004, someone connected me with “Miss Katy.” Wiest (who worked with Y‑12 Environment, Safety, and Health then) took Miss Katy on a tour of her old work location.
“It looks so different. It brings back memories … some very good ones,” she said in an interview after the tour. Wiest coordinated the tour with an ORNL employee who said he was glad to meet the namesake of his workplace and told Miss Katy, “I thought you were a myth!” (Before coming to Y‑12, I worked at ORNL for 10 years and had never heard of Katy’s Kitchen.) Miss Katy became a friend to me and attended my wedding in 2006.
While Miss Katy didn’t have a direct Y‑12 tie, she indirectly did through the renaming of a facility. In mid‑April, I found out her great, great nephew, Griffin W., works at Y‑12. He shared his aunt passed away earlier in the month and knew Miss Katy had many ties to the Oak Ridge Reservation.
Witt said, “Even at 100 years old, she would sit with me and tell me stories for hours about working out there and how much it meant to her that I too was working in Oak Ridge — supporting the mission as she once did.”
Mick Wiest and Kathryn Odom Howard visit Katy’s Kitchen in August 2005.
Little did I know when I took on a United Way Campaign project I would experience Y‑12 history with three greats, Wiest (who passed away in 2024), Smith, and Howard.
As Smith said to me in 2004, “We can be proud of the heritage of our Y‑12 history and one of the many interesting stories associated with structures that were part of the tremendous Manhattan Project that helped win both World War II and the Cold War!”
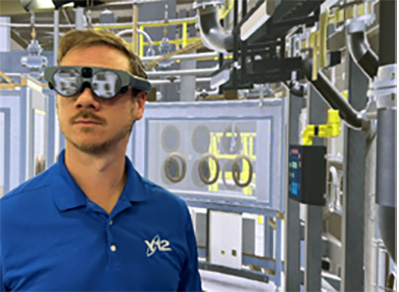
The Y‑12 National Security Complex places trainees in fully immersive virtual environments with next‑generation technologies.
It was a crazy idea, inviting the world’s best Gran Turismo gamers to get in the driver’s seat of a 600-hp Nissan GT3 to become professional race car drivers. So crazy that it actually worked. It worked because Sony’s Gran Turismo acted as extended reality (XR), a simulator that honed in the gamers’ driving skills at high speeds.
Born to be a premier facility for training in emergency response, nuclear security, and advanced technologies, the Y‑12 National Security Complex’s Oak Ridge Enhanced Technology and Training Center (ORETTC) uses XR in a similar way to train in scenarios that would be dangerous if done in the real world.
The Emergency Response Training Facility on the ORETTC campus not only focuses on training first responders but also on training Y‑12 operators on low‑occurrence, high‑consequence scenarios by using next‑generation technology, such as augmented reality, virtual reality, mixed reality (MR), and haptic feedback gloves. Funded by the Plant Directed Research, Development, and Demonstration (PDRD) program, these XR training simulations are best‑in‑class and act to fully immerse the trainee into a virtual environment through the use of these next‑gen technologies coupled with high‑fidelity digital twins developed in simulation engines such as Unreal Engine and Unity. These simulations are identical to real‑world physical spaces, persons, processes, systems, and products.
“Advances in XR have already changed the way we work, live, and play, and it’s just getting started,” PDRD Program Manager Mark Richey said. “XR literally takes ‘hands‑on’ to a whole new level. We are excited to be part of such research.”
Digital Twins and Internet of Things
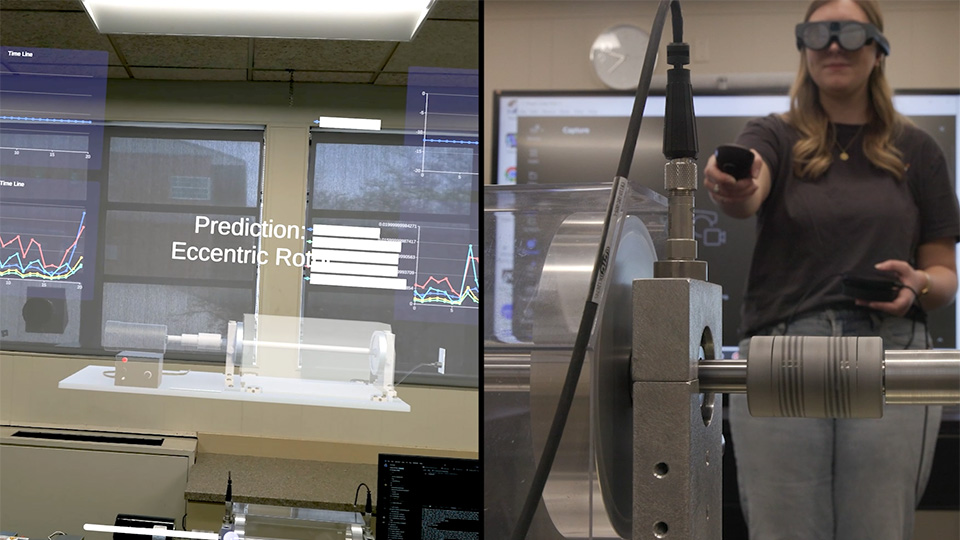
A University of Tennessee student operates a motor remotely through an XR headset and hand controllers while collecting data about the motor’s functionality.
ORETTC has unlocked Internet of Things capabilities in highly secured environments by developing a complex system engineering ecosystem that enables virtual XR headsets to access and retrieve data from real devices in a separate location. “We are able to remotely operate a motor,” said Mary Lin, interim director of ORETTC. “We can be here at ORETTC and turn on that motor at our partner facility at the University of Tennessee, Knoxville, to gain pertinent data. It’s pretty exciting.”
“The purpose of the Digital Twins and Internet of Things project is to send virtual commands to a device and also be able to read live data from a physical device as it runs,” explained Austin Arnwine, instructional technology lead. “This information loop will enable us to predict maintenance needs on machinery before it requires maintenance and even send the responsible operator the most up to date training needed to fix the machine before it needs it.”
“Y‑12 is developing digital twins at various scales,” said Scott Couture, senior director, Production Research, Development, and Integration, adding that the investment also helps create tools for other projects. “Digital twins are tools. They are a simulation at some level to help you solve a problem, such as improving the capacity and reliability of a machine.”
ORETTC applies new technology and science in a very short time frame with the goal of obtaining end products so when XR technology or machine learning advances to the next level, the technology can be integrated quickly.
“It’s so exciting! We’re not just doing the technology and science but also the application of that technology in a very short time frame,” added Tom Berg, joint adjunct assistant professor at the University of Tennessee, Knoxville. “We want to take this XR technology and machine learning to produce end products and reduce it in practice. It has so many applications outside of Y‑12!”
Collaborative XR
In the workforce today, XR is being used in many ways to collaborate with people in person and at a distance. A great example is a surgeon on the east coast who can consult with a peer/surgeon on the west coast using a secured network. This XR technology enables the ability to operate or work with a patient and meet their needs in real time while another professional is on the line.
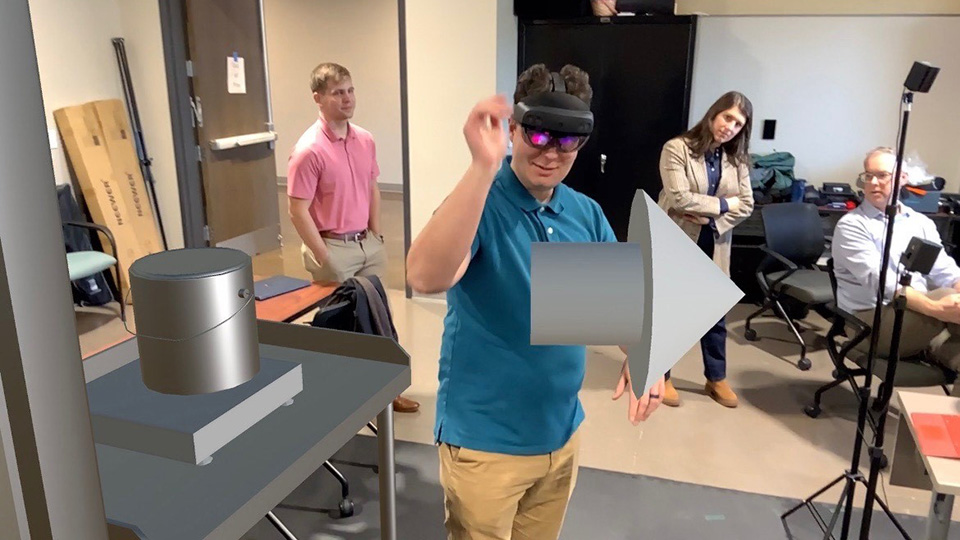
An operator is showing virtual additive manufacturing capability in a collaborative XR environment.
“The Collaborative XR project is about humanizing digital data,” explained Erik Nykwest, Y‑12 Development multi‑physics scientist. “You can set your digital asset on the table side by side with your real‑world product and compare them. You can pick up data with your hands and literally stick your head inside of it, exploring it in ways you would have never dreamed of with a two‑dimensional computer monitor. XR is an enabler that allows people to interact with digital objects as if they were real, and the collaborative aspect enhances communication and clarity when discussing complex topics.”
ORETTC has enabled this capability for additive manufacturing through funding from PDRD. Using a collaborative XR platform, ORETTC can now use headsets, tablets, and computers to convert traditional computer‑aided design (CAD) and computed tomography (CT) scans into 3‑D visuals for manufacturing and production team collaboration. This capability enables the ability to troubleshoot operations efficiently and to make design decisions without any interruption on the shop floor. These collaborations and consultations can be done in person and at a distance, as ORETTC can ship headsets to other Nuclear Security Enterprise sites for end users to collaborate as if they are in the same room.
“This technology is an evolution of how people work together moving forward,” said Arnwine. “Collaborative XR will facilitate real‑time improvements in processes and products without the need of building complex physical test models or travel for in‑person meetings.”
“For a designer or technician to be able to see what’s happening with a product or system without being in the same room is a game changer,” said Derick Weis, assistant PDRD program manager. “These platforms will facilitate real‑time improvements in processes and products.”
Haptic Feedback in Mixed Reality Glovebox Training
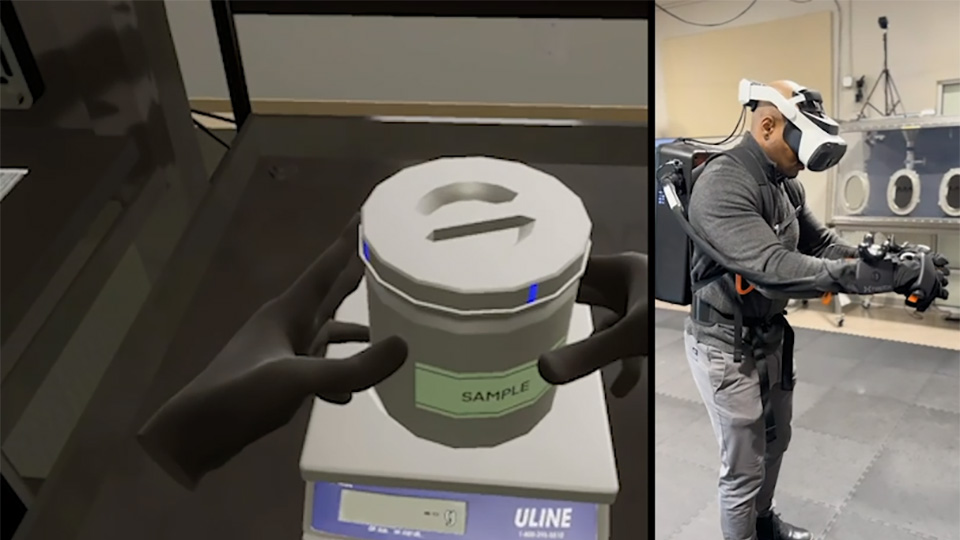
Using haptic feedback, a Y‑12 trainee works virtually to gain an understanding of the parameters of working within a glovebox.
The sense of touch and its subsequent feedback is a natural sensation often missing in XR experiences. Due to the nature of the U.S. Department of Energy’s manufacturing, dealing with sensitive materials through gloveboxes is highly touch‑driven. These glovebox jobs can be very high consequence, depending on the materials handled. ORETTC has spent the past 3 years perfecting a simulation that enables the sensations of force and texture feedback in the hands of end users in an XR training experience.
“Through the multi‑sensory engagement (touch, pressure, texture, and resistance) offered by the haptic feedback glove, chemical operator trainees feel immersed in real‑life situations while practicing conduct of operations, following procedures, and learning how to handle unlikely, but high‑stress, critical situations,” said Kim Nickell, Production Activities Training manager. “Trainees have the opportunity to practice high‑risk scenarios without real‑world consequences. Trainers are able to work with participants until the desired outcome is achieved, all while providing immediate feedback on decisions and actions that are made.”
This training experience uses haptic feedback gloves, an MR headset that the U.S. Department of Defense commonly uses for flight simulators, and a physical glovebox to simulate a material sorting exercise for new glovebox operators. This training is now being considered for placement in the Y‑12 training pipeline, as it has been tested and approved by the Y‑12 Training group and their leadership. This work was also published in “Frontiers in Virtual Reality” in March 2025 (Frontiers | VR haptics for glovebox operations training).
“With haptics in our training arsenal, trainees are getting an instructional experience that feels real,” said Weis. “It’s getting the trainees up to speed faster than traditional training methods.”
“It has been a privilege for our Production Activities Training team to work with ORETTC in the development of the Haptic Feedback Glovebox Training,” stated Nickell. “We are excited to see the future of training at Y‑12 as we adopt cutting‑edge technologies.”
Advancing XR Research and Development
“PDRD is honored to support ORETTC’s commitment to researching and developing new XR technologies and how those technologies could directly advance the manufacturing industry and NNSA’s core mission,” concluded Richey. “Through exploration of cutting‑edge solutions in immersive digital twins, haptic feedback systems, collaborative XR, and next‑generation XR environments, Y‑12’s ORETTC is driving innovation and addressing real operational needs.”
These advancements enhance workforce readiness, improve safety, increase precision, and streamline complex processes. Through strategic partnerships and forward‑thinking research, Y‑12 lays the groundwork for a more agile, capable, and future‑ready manufacturing ecosystem. Our efforts ensure that we remain at the forefront of technological progress, shaping the industry and setting new standards for excellence.
Terra M. is a night shift carpenter on the UPF Project and is one of many traveling craft professionals working at the site.
The road less traveled has proven to be a path to leadership for Terra M.
Terra is a night shift carpenter on the UPF Project and is one of many traveling craft professionals working on the site. In construction for 18 years, her career began in Alabama when her brother‑in‑law introduced her to the local union.
“I needed a job that would help support my family, and he took me right down to the union hall. I was immediately hired. I didn’t know anything, but I spent 4 years as a union apprentice and they taught me everything,” she said.
Once she was trained as a carpenter, she left Alabama and began traveling the country honing her craft. From Pennsylvania to Minnesota, Terra worked at nine different sites before joining the UPF Project in 2022. At UPF, she was invited to participate in the Craft Based Leadership (CBL) program, where she discovered herself on a new and different road.
“I’ve never worked in a place that is so supportive and treats me so well,” she said.
Since joining the CBL team, Terra has found a love of teaching. She said the CBL program allows her to coach in every craft, and she finds a way to connect with everyone.
“I always start the conversation by asking how someone is doing. I want to make sure that they aren’t carrying something into work that could become a safety issue. I care about each person,” she said.
Her motivating factor is helping people, and she takes pride in carrying the responsibility of leadership.
“I’m the leader of my family, and I feel the same way about the people I work with. They are my family, and I try to encourage them every day,” she said, noting that she has three ‘E’s for leadership. “I want to engage, encourage, and excel with everyone I talk to. It is important to me that everyone leaves the job site healthy and whole.”
In a competitive construction field, Terra has faced her fair share of challenges, but she keeps a good perspective.
“Being in this field can be rough,” she said. “You have your ups and downs, especially when you are trying to figure out what you are good at. You have to weather the storm, and, after 18 years, I have finally weathered that storm. UPF is the best place I’ve worked.”
Terra’s perspective and talent has made an impression on her managers and site leadership.
“She is the model for what we look for in CBL members," said Night Shift Environmental, Safety, and Health Lead Redd J.. “She is dedicated, knowledgeable, has a field presence, and is a great communicator. Terra is a courageous leader, who always has a great attitude. She is consistent and intent on absorbing as much knowledge and understanding as she can and upholds the standards of safety. For her, not even the sky is the limit.”
“Terra has become an integral part of our Night Shift Construction team,” added Sam B., Night Shift Construction manager. “She works tirelessly to coach our evolving and growing workforce, takes the lead in our Craft Based Leadership team, and supports a highly successful and safe night shift ES&H program.”
She goes home every month or so to her family and to her community, where she hopes to inspire others to take the road less traveled. One of her proudest moments came when her nine‑year‑old niece was in a pageant; when the panel asked Terra’s niece what she wanted to be when she grew up, she said she wanted to be “a carpenter like my auntie.”
Terra said her advice to those who are considering going into construction is to take time to explore.
“Find things out for yourself. Don’t let others determine what you want in life. The road is tough, so stay focused, stay encouraged, and don’t give up. Remember, every place isn’t for everybody, so don’t let someone discourage you from going somewhere new, just because they said so. Find out for yourself.”