Y-12 Blog
UPF Electrician inspects wiring in the 13.8kV switchgear (Per work assessment and STAART card requirements gloves are not required during the activities pictured)
Transformers are humming at the Uranium Processing Facility (UPF) as the project successfully energized medium voltage power to the Mechanical Electrical Building (MEB) during the month of June. This energization was the first connection to the Pine Ridge Substation, which the project completed in December 2019, and represents permanent power to the site.
The MEB plays the vital role of distributing power to the UPF Project. With project equipment previously running on temporary construction power, the achievement of this energization marks another step towards system operations as the MEB continues to finalize construction and progress through its testing and start-up phase.
“This energization required months of coordination between multiple entities, which included BNI Startup, BNI Engineering, CNS AHJs (authority having jurisdiction), CNS Power Operations, Subcontractors and numerous others,” said Jeremy Wilkins, UPF Start-Up Manager. “The UPF project team put in countless hours demonstrating the dedication and quality of work needed to successfully achieve this significant project milestone. It was a job well done and most importantly, it was a job done safely,”
The UPF Project successfully energized Medium Voltage Power in the Mechanical Electrical Building
“Thank you to all of our team members who made this happen. We have come a long way from what once started as a parking lot and that is solely because of every individual’s efforts on the UPF Project,” said Dena Volovar, UPF Project Director.
As the project progresses, the medium voltage power system will supply power to both the process and utility systems in the MEB, as well providing power to the other UPF buildings such as the Main Process Building and the Salvage and Accountability Building.
Accepting the Star of Excellence award plaque from Gene Sievers, Y-12 Site Manager, is Mike Thompson (left), president of the Atomic Trades and Labor Council, with members of the safety team and their representatives in attendance.
Y-12 recently received the Voluntary Protection Program (VPP) Star of Excellence Award from the U.S. Department of Energy (DOE). VPP promotes safety and health excellence through cooperative efforts among labor, management, and government at DOE contractor sites.
The award plaque states the following:
Through their full dedication and total commitment to the principles of VPP, they have achieved an outstanding level of performance in meeting established safety and health goals, actively conducting outreach to others, and in achieving an injury and illness rate significantly below the average of similar businesses and operations.
Gene Sievers, Y-12 Site Manager, expressed his appreciation to the team for their efforts to increase employee engagement in safety awareness. He said, “With the safety stats we’re seeing, it makes you feel good. In part, that is thanks to the work of this team.”
Thanks to teamwork, a plan to restore power during a scheduled outage kept the mission on schedule.
It’s hard to get much work done without power. That’s especially true at Pantex and Y-12, where power needs drive many production processes and where any loss of power can result in missed schedules and deliverables. At Y-12, managers faced that very problem. A failed transformer was threatening to delay important mission work that could have impacted deliverables and more than 150 workers.
“Even with a spare temporary transformer on hand, we feared it might take several weeks to retrofit the spare into this installation,” said Susan Baker, Fabrication Operations director. “We needed a solution fast.”
The solution came from the Power Operations Preventive Maintenance Program and a team of more than 100 craft, staff members, supervisors, and managers. The Power Operations team quickly developed a plan to restore power during a scheduled outage. The team identified an alternate location for the temporary transformer that required minimal modifications and developed a way to complete the process that shortened the duration of the outage. In addition, Infrastructure provided temporary lighting and power to enable some operations to resume during the week of the outage.
“We were back to full operations on the following Monday,” Baker said. “With help from many organizations, we recovered our production schedule and met our monthly deliverables.”
The effort went so well that the team was recognized by the Y-12 Safety Council, which awarded the group the site manager’s monthly safety award. The Safety Council said, “This team worked together to meet the common goal with zero injuries and without incident.”
The effort also demonstrated the importance of the Power Operations Preventive Maintenance Program. It required a tremendous amount of coordination and teamwork that was on full display during the installation of the temporary transformer.
“I want to thank every person who worked diligently during the outage,” said Ellis Scruggs, Power Operations System Health manager. “This project exemplifies what can be accomplished when we all work together for mission success.”
Welder Joel Chavez welds a tooling fixture.
Y-12’s can do attitude is legendary. Perhaps the men and women of General Manufacturing Operations best exemplify that mindset.
“If it can’t be done anywhere else, bring it to us. We can do it,” said Wendell Laughter, a production specialist with 16 years of experience in Building 9201 1, known as Alpha 1. “We’re a one stop shop.”
We do it all … well, almost
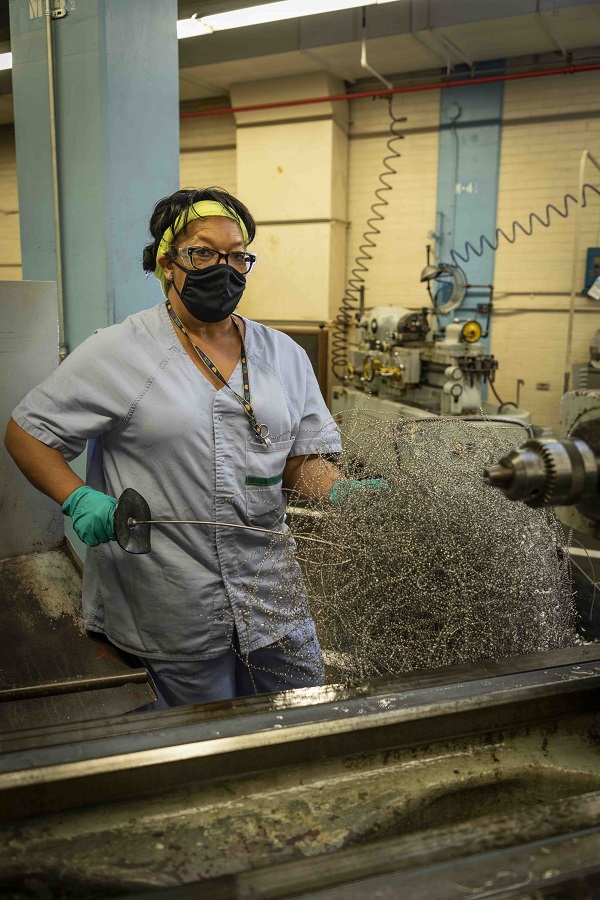
Laura Dye, machine cleaner, removes chips from a lathe.
GMO sheet metal fabricators, machinists, and welders cut, bend, saw, grind, punch, melt, and join metal into the desired shape and design. Using manual and computerized numerical control lathes and mills, they work with nickel, bronze, lead, aluminum, titanium, copper, and many other metals, plastics, composites, graphite, and special materials. GMO's skilled craftspeople can machine and fabricate parts weighing several tons with tolerances to 1/10,000 of an inch.
“We create the specialty tooling, fixtures, and shipping containers for all of Y-12’s weapons programs,” said John Sarratt, a production support specialist. “We also have about 200 or so walk in work orders a year when things break down across the site, everything from unique ductwork to filter crushers to door handles that resolve safety actions.”
“I support the Y-12 mission by keeping the machines oiled and lubricated and ready for use at all times.” —Larry Seiber, machine oiler
“I like my coworkers and fabricating different parts to support our nation.” —Randles Solomon Jr., sheet metal worker
“I use traditional equipment, such as mills, lathes, and grinders, to produce high quality products for our customers. What I like best about my job are my coworkers and the type of work we do.” —Daniel McPeek, machinist
“Through the years, we made the parts for the weapons and now we make the fixtures to continue making the parts and the containers to ship them. I like the people who I work with and the feeling of family out here.” —C.D. Hill, machinist
Recently, a gear failed in an on site transformer critical for plant operations. There was no clear path forward on how to get it fixed. The gear would be difficult to procure, if it could be procured at all. So, the Y-12 customer brought the broken gear to GMO.
“We didn’t have drawing specifications for the part, only the piece itself,” Laughter said. “Our folks were able to not only recreate the piece and make critical spares for potential future failures but also turn it around quickly.”
In addition to its Y 12 work, GMO has many external customers. For years, Nuclear Security Enterprise sites (including Pantex and Lawrence Livermore National Laboratory), federal agencies, and industry have been coming to Y-12 to do what couldn’t be done. Sometimes GMO's handiwork shows up in celebrated tools and machinery. For example, GMO built the first propulsor for the U.S. Navy’s Seawolf class nuclear submarine. The Navy–Y-12 prototyping team responded to more than 1,000 design changes in less than four years.
Skill of the craft
Even with the most advanced machines in the world, it is the skill of the craftspeople that makes GMO especially adept at creating first of a kind products.
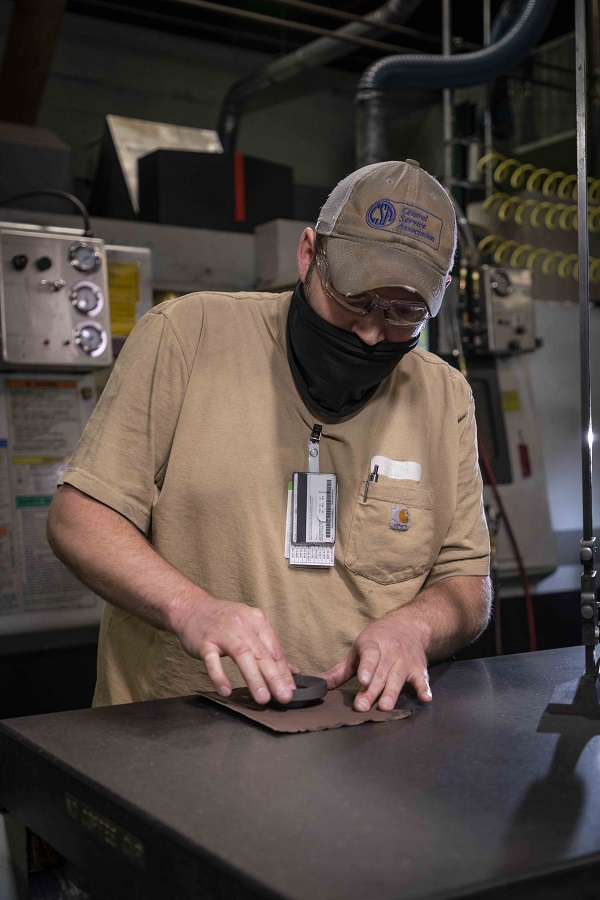
Machinist Justin Acres sands a graphite part flat on a surface plate.
“We work on a variety of one off parts, so we have a lot of opportunities to learn and grow in our craft without being confined to working on the same part or job over and over,” said Ashley Dawson, a machinist who joined Y-12’s apprenticeship program in 2013.
In Y-12’s defense work, the manufacturing shop must follow technical procedures. When pioneering new products, however, craftspeople simply go by sketches and drawings.
“Working in Alpha 1 allows a machinist to become well rounded within our craft, given that we are able to machine our parts, for the majority, without being confined to a procedure,” said Mike Trexler, also a machinist from the 2013 apprenticeship program. “Unlike a production shop, we seldom run multiples of the same part, so we’re always making different parts and using different materials.”
Made in the USA
In addition to a can do attitude and skill, Y-12’s manufacturing craftspeople take unmistakable pride in their workmanship and the site’s national security mission.
“We all take ownership and pride in our work,” said supervisor Ray Ivey, who’s spent most of his 52 year career at Y-12 in Alpha 1. “We work together as a team to get the job done safely and with quality, and this is what’s made us successful.”
Machinist Kent Sellars agreed that Alpha 1 turns out a better product because of the team approach to national security work. “To be able to share in this incredible depth of talent and experience is a great honor,” he said. “The importance of our national security mission drives me to want to be the best machinist I can be. This allows me to serve each day as a working patriot in ensuring that each assignment is completed within the desired scope of the design and forethought of each project.”
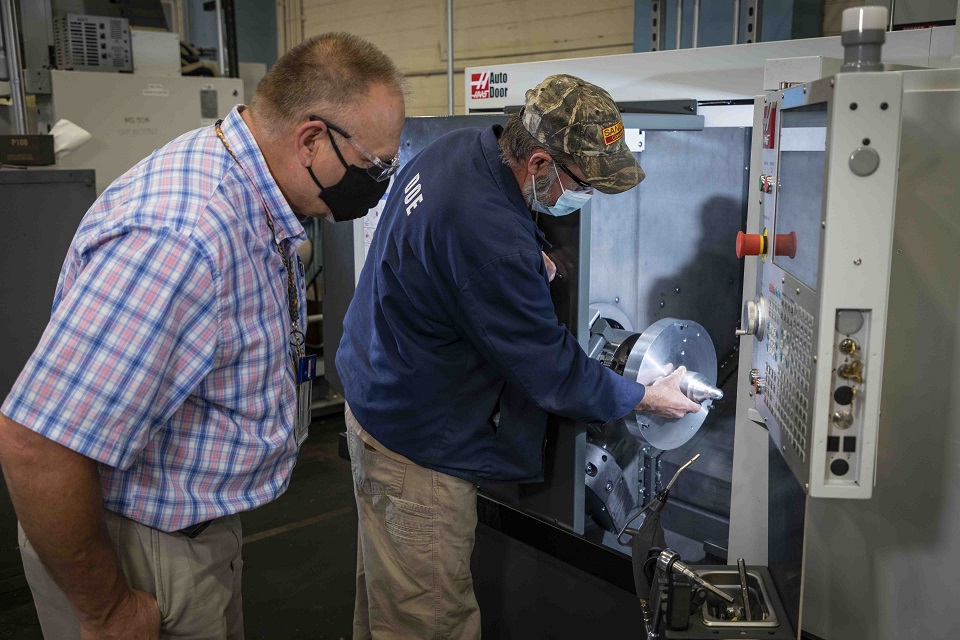
Production specialist Wendell Laughter, left, and machinist Mike Montgomery set up a computerized numerical-control lathe.
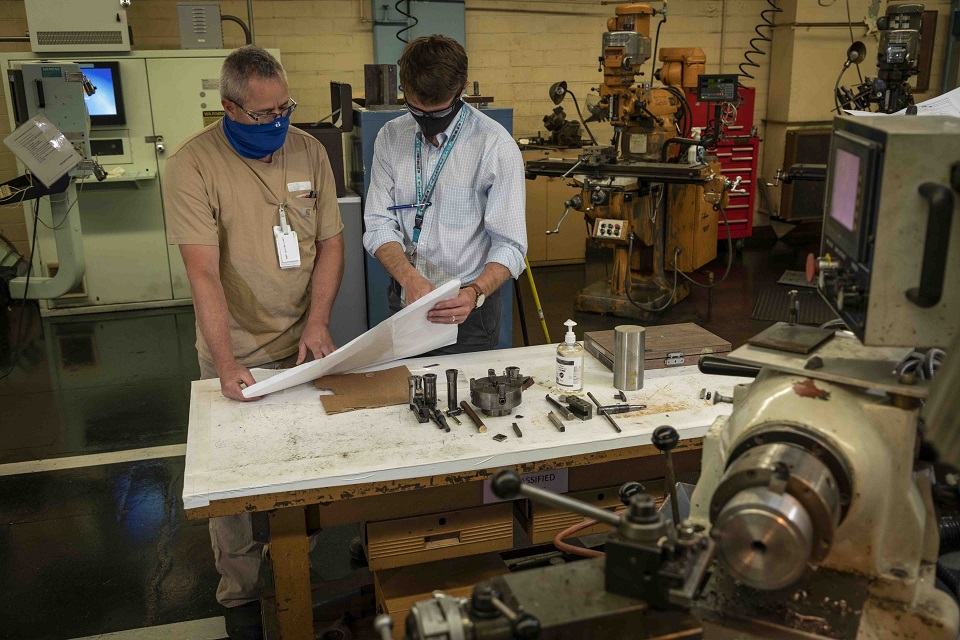
Machinist Randy Golliher, left, and Erik Swanson, GMO production support manager, view a tooling drawing. “I like the people I work with, knowing that I’m making parts for our nation’s defense, and doing my job as safely as possible,” Golliher said.
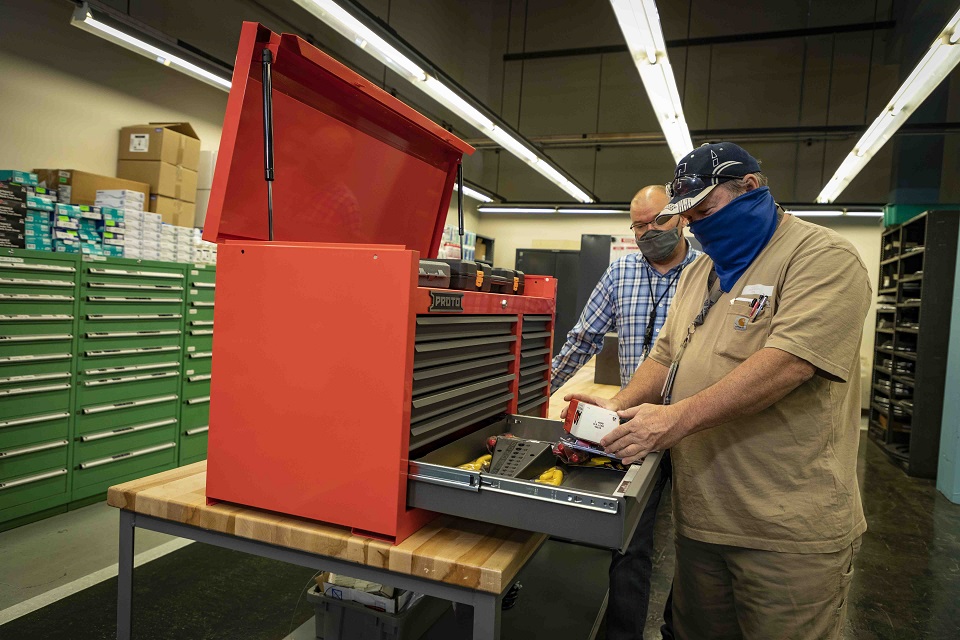
Supervisor Jeff Prince, left, and machinist Chad Huff sort through a tool box in the tool crib.
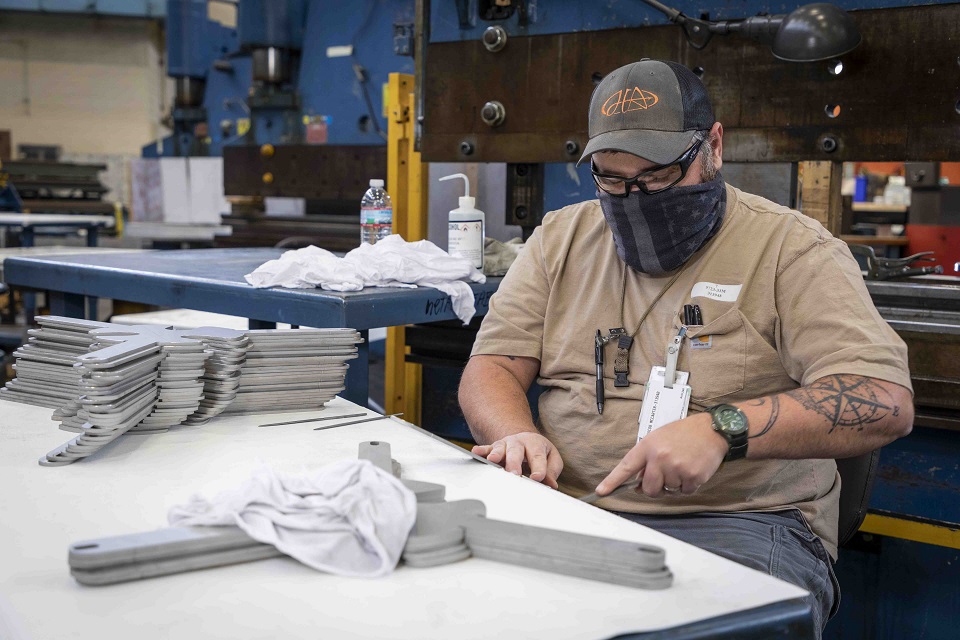
Sheet metal worker Jacob McCarter works on a fixture component in metal fabrication.
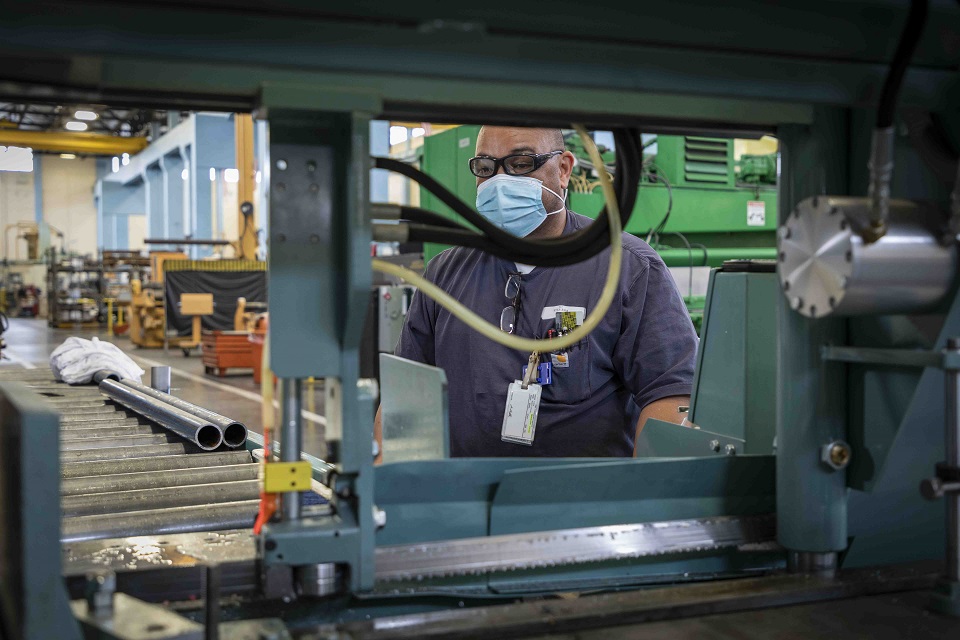
Sheet metal apprentice Monty Stovall saws tubing. “I really like my coworkers and the challenges of fabricating metal,” Stovall said.
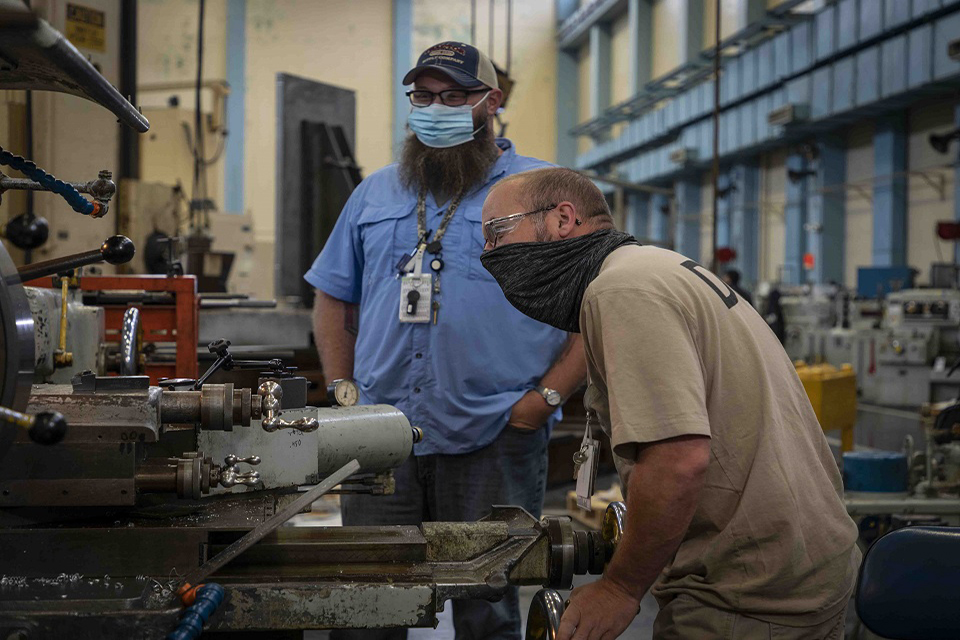
Kevin Lewis (left), a production support specialist, and machinist Matt Bumbalough turn a component on a manual lathe.
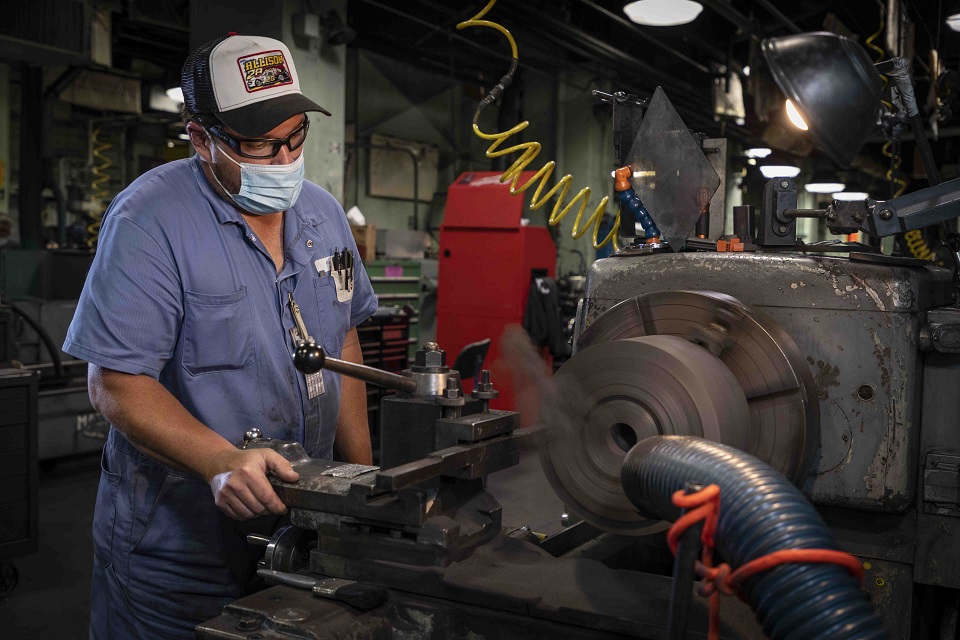
Machinist Mike Trexler turns a graphite component on a manual lathe.
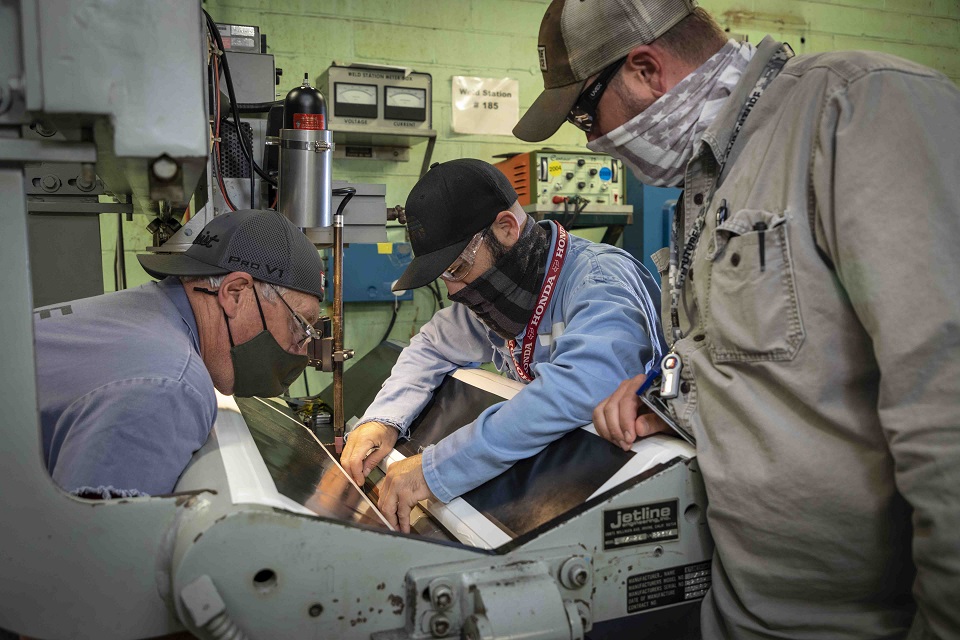
From left, sheet metal worker Rick Valentine, welder Levi McDaniel, and machining supervisor Mike Woosley set up a welder in the can shop.
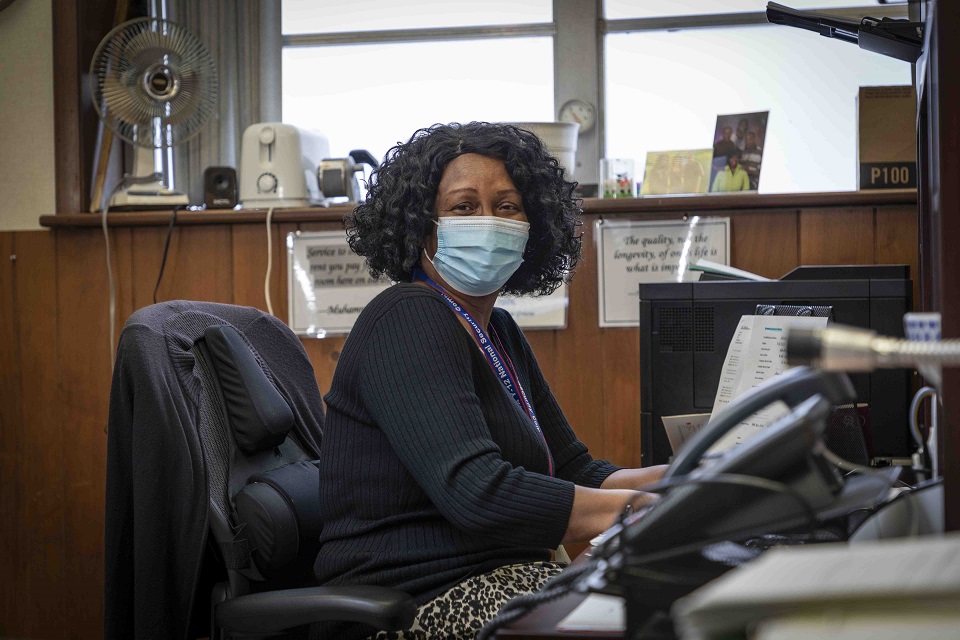
Administrative professional Sherry Hill supports all of General Manufacturing Operations, among other duties.
Emory Valley Center staff members are appreciative of the grant from CNS that was used to purchase personal protective equipment for employees.
CNS continues to look for ways to help our communities toward recovery as the COVID-19 pandemic eases its grip. The company recently turned to the East Tennessee Foundation and its Neighbor to Neighbor Fund to join with the CNS Community Investment Fund. Together, we were able to quickly get much needed resources to several nonprofit organizations in East Tennessee.
Emory Valley Center
Emory Valley Center supports about 3,000 people every year in multiple East Tennessee counties through behavioral health, community integration, education, employment, family assistance, prevocational training, and residential services. Often these clients have intellectual, developmental, and physical disabilities. Providing direct residential care to these clients during the pandemic meant that EVC employees became essential employees who required personal protective equipment to perform their jobs. When the pandemic started, the center had only enough personal protective equipment to supply one staff member for one week.
Thanks in part to a $2,500 grant from CNS, direct care continued safely with much needed PPE and additional hazard pay for some EVC employees.
“With these funds, in addition to other grants secured, EVC was able to provide a safer work environment and help compensate our frontline employees for putting themselves at risk when caring for people we support,” said Jennifer Enderson, EVC president.
The center provides residential support (in-home care) to 103 people living at 51 residential sites in Oak Ridge and surrounding areas. Over the past year, prices for masks increased from less than $1 each to $6 each. To safely perform its duties, EVC estimated that 1,695 masks and other protective equipment for direct care staff would be needed. Grant money helped make that possible.
“Even though we were fortunate the COVID-19 vaccine was available for people we support and staff in late January and mid February, we continue to be diligent with safety protocols recommended by the CDC,” said Enderson. “It’s imperative to have enough supplies and create the safest work environment possible for our essential staff while ensuring the people we support are cared for safely during the pandemic.
“We are grateful for the support for Emory Valley Center, particularly in such a challenging time while the pandemic occurred and is ongoing,” she added.